The Critical Role of Vibratory Screens in Pharmaceutical Processing
Understanding Pharmaceutical Intermediates and Their Importance
Pharmaceutical intermediates serve as the foundational building blocks in drug manufacturing. These chemical compounds undergo multiple processing stages before transforming into active pharmaceutical ingredients (APIs). Maintaining the highest level of purity in these intermediates is critical, as even the slightest impurity can compromise the safety and efficacy of the final drug product. Ensuring proper handling and refinement through efficient screening techniques is paramount to meeting regulatory and quality standards.
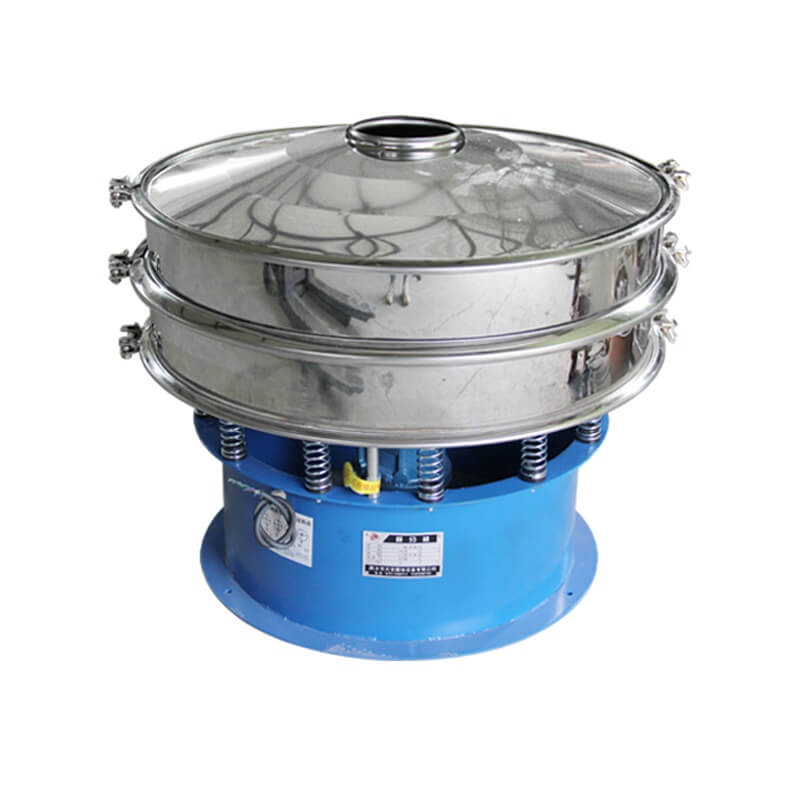
How Vibratory Screens Enhance Purity and Consistency
Vibratory screens play a pivotal role in refining pharmaceutical intermediates by separating unwanted particles, ensuring uniform particle size distribution, and enhancing material homogeneity. These specialized sieving systems leverage vibratory motion to filter out oversized or undersized particles, preventing contamination and improving batch-to-batch consistency. This level of precision is crucial in achieving the stringent purity levels required in pharmaceutical production.
The Impact of Precise Sieving on Drug Safety and Effectiveness
Inconsistent particle sizes or foreign contaminants can affect the dissolution rate, absorption, and overall effectiveness of a drug. By utilizing high-precision vibratory screening equipment, pharmaceutical manufacturers can achieve uniformity in their intermediates, thereby ensuring consistent bioavailability and therapeutic efficacy. Moreover, adherence to strict quality control protocols through effective sieving mitigates the risk of defective batches and regulatory non-compliance.
Key Advantages of Using Vibratory Screens for Pharmaceutical Intermediates
Eliminating Contaminants and Foreign Particles with High-Precision Screening
The presence of foreign particles in pharmaceutical intermediates can pose serious health risks and compromise drug formulation integrity. Vibratory screens act as a frontline defense by efficiently removing unwanted contaminants, from dust and agglomerates to extraneous materials. This meticulous separation process helps manufacturers maintain the highest standards of product purity and safety.
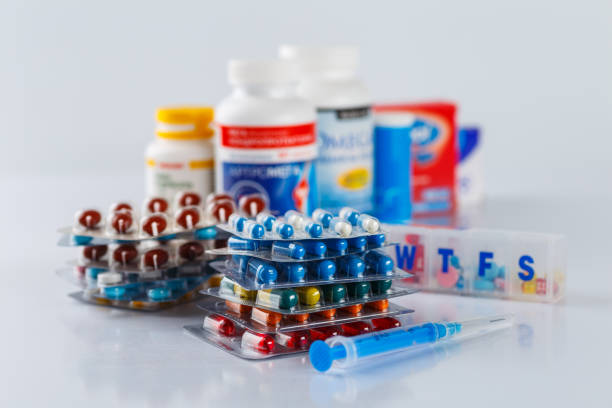
Improving Production Efficiency and Reducing Material Waste
Efficient sieving contributes to optimized raw material usage, reducing unnecessary waste and ensuring maximum yield. By employing vibratory screens, pharmaceutical companies can streamline their production processes, minimize downtime, and enhance throughput. The automation and adaptability of these screens allow for continuous operation, reducing labor costs and improving overall operational efficiency.
Achieving Uniform Particle Size Distribution for Better Formulation
Uniformity in particle size distribution is essential for achieving consistent drug formulation and performance. Vibratory screens help in standardizing intermediate particle sizes, leading to improved flowability, solubility, and compressibility. This is particularly important in tablet formulation, where consistency in granule size directly impacts tablet strength, disintegration, and dissolution properties.
Optimizing Vibratory Screening for Pharmaceutical Applications
Selecting the Right Vibratory Screen for Different Pharmaceutical Intermediates
Choosing the appropriate vibratory screen depends on the specific characteristics of the pharmaceutical intermediate being processed. Factors such as particle size, moisture content, bulk density, and flow properties should be considered when selecting screening equipment. Additionally, compliance with Good Manufacturing Practices (GMP) and other regulatory guidelines is crucial in ensuring that the chosen screen meets industry standards.
Best Practices for Maintaining and Calibrating Vibratory Screens
Regular maintenance and calibration of vibratory screens are necessary to sustain their efficiency and accuracy. Cleaning the mesh, inspecting for wear and tear, and ensuring proper tensioning of screen panels can prevent operational inefficiencies. Scheduled calibration checks also help in maintaining consistent screening precision, avoiding deviations that may lead to product inconsistencies.
Overcoming Common Sieving Challenges in Pharmaceutical Manufacturing
Despite their advantages, vibratory screens can face challenges such as mesh clogging, material buildup, and screen degradation. Employing ultrasonically assisted screening, anti-blinding devices, and appropriate mesh selection can mitigate these issues. Additionally, integrating dust containment systems ensures compliance with safety standards, preventing cross-contamination and exposure risks.
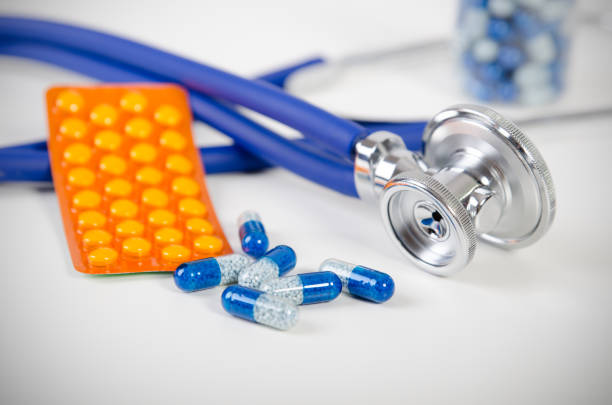
The Future of Vibratory Screening in the Pharmaceutical Industry
Innovations in Vibratory Screen Technology for Pharmaceutical Processing
Technological advancements in vibratory screening are continuously enhancing pharmaceutical processing efficiency. Developments such as ultrasonic sieving, self-cleaning screens, and real-time monitoring systems are revolutionizing the industry. These innovations enable higher precision, reduced downtime, and improved adaptability to complex screening requirements.
The Role of Automation in Enhancing Screening Efficiency
Automation is transforming vibratory screening by integrating AI-driven control systems, remote monitoring, and predictive maintenance features. Automated screening solutions reduce human intervention, enhancing repeatability and minimizing errors. This level of precision is vital in pharmaceutical manufacturing, where regulatory compliance and quality consistency are non-negotiable.
How Advanced Sieving Techniques Will Shape the Future of Drug Manufacturing
As the pharmaceutical industry evolves, the demand for more refined sieving techniques will continue to grow. The adoption of advanced vibratory screening systems will play a crucial role in meeting stricter regulatory requirements, improving production efficiency, and ensuring higher drug quality. Future trends indicate a shift towards eco-friendly and energy-efficient screening solutions, further aligning with the industry’s sustainability goals.
Vibratory screens are indispensable in pharmaceutical intermediate processing, ensuring purity, efficiency, and compliance with stringent industry standards. Their role in maintaining high-quality drug formulations underscores their importance in modern pharmaceutical manufacturing. By investing in cutting-edge vibratory screening technology and adhering to best practices, pharmaceutical companies can achieve superior product consistency, regulatory compliance, and enhanced operational efficiency.