Understanding the Role of Vibrating Screens in Sulfur Powder Processing
Overview of Vibrating Screens and Their Functionality
Vibrating screens are integral components in many industrial processes, particularly in the classification and separation of particles. These machines use controlled vibrations to sort materials into different grades or sizes based on their unique properties. In the case of sulfur powder, a fine, granular substance, vibrating screens help segregate it into various sizes for further processing, packaging, or use in chemical applications. The screen mesh is vibrated in such a way that particles of a certain size can pass through the mesh, while larger or unwanted particles are left behind.
These machines operate on a simple principle: vibrations are generated either through a motor or an electromagnetic mechanism, causing the screen mesh to move in a rapid, rhythmic motion. This motion facilitates the movement of materials across the surface of the screen, allowing fine sulfur powder to filter through while larger particles remain on top.

How Vibrating Screens Enhance the Sifting Process for Sulfur Powder
Sulfur powder, owing to its fine particle size and unique chemical properties, demands precise handling during sifting. The vibrating screen enhances this process by ensuring that the sulfur powder is sifted with high efficiency and accuracy. The vibrating motion helps break up any clumps or agglomerates, allowing the powder to be separated uniformly according to particle size. This makes the process of sorting sulfur powder much more effective compared to traditional manual methods or static screens.
Additionally, the vibration helps to prevent clogging of the mesh. Sulfur powder, being highly reactive, can sometimes cause materials to stick to the mesh, reducing efficiency. The constant movement of the screen ensures that the powder does not settle on the mesh or block the pores, thus maintaining a continuous and smooth separation process.
The Importance of Vibration in Achieving Accurate Separation
Vibration plays a crucial role in achieving the desired level of separation in vibrating screens. The intensity, frequency, and amplitude of the vibrations are all carefully calibrated to optimize the sorting of sulfur powder. Proper vibration ensures that the particles move in a controlled manner across the screen, reducing the chances of particles becoming trapped or inaccurately classified.
Moreover, the right balance of vibration minimizes the wear and tear on the equipment while maximizing throughput and screening accuracy. The vibrations must be strong enough to push the powder through the mesh but not so forceful as to cause excessive damage to the delicate powder or the machine itself.

The Science Behind Screening Accuracy in Sulfur Powder
How Screening Accuracy Affects Product Quality and Consistency
Screening accuracy is paramount in sulfur powder processing, as it directly impacts both the quality and consistency of the final product. When sulfur powder is not accurately sifted, it can lead to inconsistencies in particle size, which can affect its behavior in downstream applications. In chemical processes, for instance, variations in particle size can result in uneven chemical reactions, affecting the efficiency and yield of the reaction.
Moreover, poor screening accuracy can also impact the packaging process, leading to unevenly sized portions of sulfur powder, which can result in customer dissatisfaction or complications in product handling. Hence, achieving high screening accuracy ensures that each batch of sulfur powder meets the strict specifications for quality, resulting in reliable, consistent products.
Factors That Influence Screening Accuracy for Sulfur Powder
Several factors influence the screening accuracy of sulfur powder. These include the mesh size, vibration parameters, feed rate, and the moisture content of the powder. The mesh size must be carefully selected to match the desired particle size distribution of the sulfur powder. If the mesh is too small, it may cause clogging, and if it is too large, it will allow unwanted particles to pass through.

Vibration parameters such as frequency, amplitude, and direction also play a significant role in ensuring the right separation. The feed rate, or the speed at which sulfur powder is introduced onto the screen, needs to be adjusted to avoid overloading the screen or causing irregular separation. Lastly, the moisture content in sulfur powder can affect its flowability, causing clumping and uneven sifting. Proper moisture control is crucial for maintaining screening accuracy.
Best Practices for Maximizing Screening Precision in Vibrating Screens
Maximizing screening precision involves both understanding and fine-tuning the various parameters involved in the screening process. First, it is vital to choose the correct mesh size based on the particle size distribution of the sulfur powder. Regular maintenance of the vibrating screen is also essential to ensure its performance stays optimal, including checking for any wear and tear or damage that may affect screening accuracy.
Secondly, vibration settings should be periodically tested and adjusted as necessary. This includes ensuring the correct amplitude and frequency, depending on the type of sulfur powder being processed. Monitoring the feed rate is also crucial. Too high of a feed rate can overload the screen, reducing its efficiency and the accuracy of the separation process.
Lastly, controlling the humidity and moisture content in sulfur powder can prevent issues such as clumping or sticking to the screen mesh. Keeping the material dry and evenly distributed will ensure smooth and consistent sifting.
Choosing the Right Vibrating Screen for Sulfur Powder Sifting
Types of Vibrating Screens Suitable for Sulfur Powder Processing
There are several types of vibrating screens that can be employed for sulfur powder sifting, each with distinct advantages depending on the application. The most commonly used types include linear vibrating screens, circular vibrating screens, and rotary screens. Linear vibrating screens offer efficient separation, with a straight-line motion that allows for precise sorting of materials based on particle size.
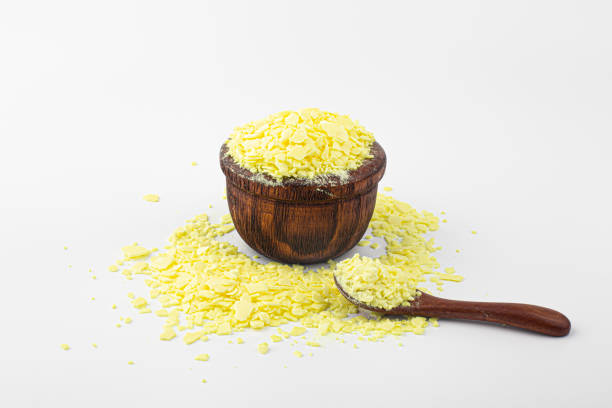
Circular vibrating screens, on the other hand, utilize a circular motion and are generally used for larger capacities. They are ideal for high-throughput applications but may not provide the same level of precision as linear screens for finer powders. Rotary screens are more suited to situations where gentle handling is required, such as in delicate or fragile materials, offering good flexibility for sulfur powder processing.
Key Features to Look for in a Vibrating Screen for Sulfur Powder
When selecting a vibrating screen for sulfur powder sifting, several key features must be considered to ensure optimal performance. First, the screen material should be resistant to corrosion, especially given sulfur powder’s reactive nature. Stainless steel is often the material of choice due to its durability and resistance to chemical reactions.
Another critical feature is the screen mesh configuration. A well-designed mesh should prevent clogging while allowing for precise particle separation. The vibratory motor should also be durable and adjustable, offering versatility to adapt to different particle sizes and production volumes. Additionally, ease of maintenance, such as accessible parts and simple cleaning protocols, should be a priority.
Maintenance Tips to Ensure Long-Term Screening Efficiency and Accuracy
To keep a vibrating screen functioning efficiently over time, regular maintenance is essential. Routine inspections should be conducted to check for any wear or damage to the mesh, motor, or frame. Lubrication of moving parts will also help reduce friction and prevent premature wear. Periodic cleaning of the screen mesh is crucial to remove any buildup of sulfur powder or other materials that could cause blockages.
Calibrating the vibration frequency and amplitude at regular intervals will also ensure the machine continues to perform optimally. Additionally, addressing any signs of imbalance in the screen immediately can prevent unnecessary strain on the motor and other components, prolonging the lifespan of the equipment. Proper storage when not in use will protect the screen from environmental damage, such as rust or moisture buildup.