The Importance of Chemical Solutions in Russia’s Industries
How Chemical Solutions Drive Industrial Growth in Russia
In Russia, the chemical industry plays a pivotal role in driving economic development. Chemical solutions are integral to a vast array of industries, from agriculture and pharmaceuticals to energy and manufacturing. The ability to provide cost-effective, high-performance chemical products enables Russian industries to meet global demand while also fostering innovation. Chemical solutions are essential for producing materials that enhance the quality of life, improve energy efficiency, and sustain natural resources. As the demand for more advanced and specialized products increases, the need for efficient, scalable production methods becomes paramount—ushering in the importance of optimized technologies, such as vibrating screens, to meet these challenges.

Key Challenges Faced by Chemical Industries in Russia
Russia’s chemical industries face numerous obstacles that hinder their growth potential. The vast geographical landscape and complex infrastructure pose logistical challenges, impacting both the distribution of raw materials and the delivery of finished products. Additionally, fluctuating raw material prices and the increasing need for sustainable practices put significant pressure on companies to reduce waste and improve efficiency. Another challenge is maintaining quality and consistency in the production process. Variability in raw materials and processing equipment can lead to subpar product outcomes, which affects both domestic and international competitiveness. Vibrating screens offer solutions to many of these challenges, particularly in enhancing the quality control aspect by ensuring the purity and consistency of chemical mixtures.
The Role of Technology in Improving Chemical Solutions
The adoption of new technologies is key to overcoming the hurdles facing Russia’s chemical industries. Automation, data analytics, and advanced separation techniques are revolutionizing the production process. Vibrating screens, for instance, provide precise particle separation and material classification, ensuring higher yields and more consistent product quality. This technological shift not only helps increase productivity but also reduces the environmental impact of production. By integrating innovative equipment like vibrating screens into chemical processing, companies can streamline operations, reduce costs, and meet the growing demands of the market.

The Power of Vibrating Screens in Chemical Processing
Why Vibrating Screens Are Essential for Chemical Solutions
Vibrating screens are indispensable tools in the chemical industry due to their ability to efficiently separate and classify materials based on size and particle properties. In chemical processing, materials are often subjected to various stages of sieving, filtration, and separation to ensure that impurities are removed, and the final product is of the desired quality. Vibrating screens offer a mechanical method of generating vibration to agitate the material, ensuring that particles are accurately classified. This process maximizes throughput while maintaining high standards of quality control. Without vibrating screens, achieving the necessary purity and consistency in chemical solutions would be challenging, if not impossible.
How Vibrating Screens Improve Efficiency and Productivity
Efficiency is a critical factor in chemical processing, particularly in Russia, where production rates are vital to meeting both domestic and international demand. Vibrating screens improve efficiency by providing continuous and uniform separation of materials. As the screen vibrates, the particles pass through mesh apertures, with larger particles being filtered out and finer particles allowed to pass through. This continuous flow reduces downtime and improves throughput, ensuring that production runs smoothly. Additionally, the automation of vibrating screens ensures consistency and reduces manual labor, allowing operators to focus on other aspects of production, ultimately improving productivity.
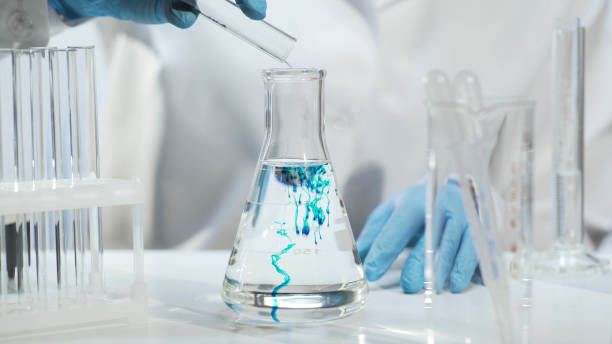
The Role of Vibrating Screens in Separating Chemical Components
In chemical processing, separating chemical components based on their size and density is essential for creating high-quality products. Vibrating screens facilitate this by offering precise separation capabilities. By adjusting the mesh size and vibration settings, vibrating screens can be optimized to handle a wide range of materials, from fine powders to coarse granules. This makes them highly adaptable to various chemical processes, such as the separation of active ingredients from impurities or the classification of materials for further refinement. The use of vibrating screens ensures that the final chemical solution is homogeneous, precise, and ready for the next stage of processing.
Advantages of Using Vibrating Screens in Russian Chemical Plants
Enhanced Product Quality and Consistency with Vibrating Screens
One of the most significant advantages of using vibrating screens in chemical plants is the improvement in product quality and consistency. The precision of vibrating screens allows for finer separation of materials, ensuring that only the desired particle sizes remain in the final chemical product. This leads to a more consistent texture, appearance, and chemical composition, which is crucial for industries like pharmaceuticals and food processing, where quality control is paramount. In the Russian chemical industry, where the demand for high-quality products is growing, vibrating screens offer a reliable solution for maintaining strict quality standards.
Reducing Operational Costs with Efficient Sieving Technology
Vibrating screens reduce operational costs by minimizing material wastage and enhancing process efficiency. By ensuring accurate particle classification, vibrating screens prevent the inclusion of impurities, reducing the need for additional processing steps. This not only saves on raw materials but also on energy consumption, as more efficient sieving allows for faster processing times. Additionally, vibrating screens are designed for durability and reliability, reducing maintenance costs and downtime. In Russia’s competitive chemical industry, reducing operational expenses while maintaining high product quality is essential for profitability.

Supporting Sustainable Chemical Solutions in Russia’s Market
Sustainability is increasingly becoming a focal point in the chemical industry, as companies are expected to reduce their environmental footprint. Vibrating screens support sustainable practices by reducing waste, improving material recovery, and minimizing the use of harmful chemicals. By optimizing the separation process, vibrating screens allow for the recovery of valuable materials that would otherwise be discarded, contributing to the circular economy. This is especially important in Russia, where the drive for eco-friendly solutions is gaining momentum. The ability to integrate sustainable technology into chemical processing is not only beneficial for the environment but also enhances the reputation of companies in the global market.
Integrating Vibrating Screens into Russia’s Chemical Industry
Best Practices for Implementing Vibrating Screens in Chemical Plants
Successfully implementing vibrating screens in chemical plants requires careful planning and integration. It’s essential to select the right screen type and mesh size for the specific materials being processed. In addition, operators should be trained to adjust the vibration settings to optimize efficiency based on real-time production conditions. Regular maintenance is also critical to ensure that screens continue to function properly and efficiently. By adhering to these best practices, Russian chemical plants can maximize the benefits of vibrating screens and improve overall operational performance.
Challenges and Solutions for Integrating Vibrating Screens in Russia
While integrating vibrating screens into Russian chemical plants offers significant benefits, there are challenges to consider. One of the main hurdles is the initial cost of investment, which may be prohibitive for smaller operations. Additionally, integrating new equipment into existing production lines may require modifications to infrastructure or workflows. To overcome these challenges, businesses can explore financing options or phased implementations to gradually transition to more efficient equipment. Collaborating with equipment manufacturers for tailored solutions and ongoing technical support can also ensure a smoother integration process.
The Future of Chemical Solutions in Russia with Vibrating Screen Technology
As Russia’s chemical industry continues to evolve, vibrating screen technology will play an increasingly important role in improving processing efficiency, product quality, and sustainability. The future of chemical solutions in Russia is one where technology and innovation drive success, and vibrating screens are at the forefront of this transformation. With advancements in automation, data analysis, and machine learning, vibrating screens will become even more precise and efficient, helping Russian chemical plants meet the demands of both local and global markets.

Maintenance and Optimization of Vibrating Screens for Chemical Solutions
Key Maintenance Tips for Vibrating Screens in Chemical Applications
Routine maintenance is vital to ensuring that vibrating screens continue to operate at peak performance. Key tasks include regularly checking for wear on the mesh and ensuring that the vibrating mechanism is functioning correctly. Operators should also clean the screens frequently to prevent material buildup, which can hinder efficiency. Regular lubrication of moving parts and timely replacement of worn-out components will extend the lifespan of the equipment and maintain consistent performance.
Optimizing Vibrating Screens for Maximum Efficiency and Output
To optimize vibrating screens, operators must monitor key parameters, such as vibration amplitude, mesh size, and feed rate. Fine-tuning these settings based on the characteristics of the material being processed will ensure the most efficient separation. Implementing automated control systems can further enhance performance by adjusting settings in real time, depending on the production needs. By continually assessing and optimizing screen performance, chemical plants can achieve maximum output while minimizing downtime and resource consumption.
Ensuring Longevity and Reliability of Vibrating Screens in Harsh Conditions
Vibrating screens are often subjected to harsh working conditions, including high temperatures, abrasive materials, and continuous operation. To ensure longevity and reliability, it’s important to select screens made from durable materials that can withstand these challenges. Regular inspections and proactive maintenance schedules can prevent unexpected breakdowns. In extreme conditions, implementing advanced monitoring systems that track screen performance and alert operators to potential issues before they escalate can help maintain optimal functioning and extend the lifespan of the equipment.