Achieving a flawless powder coating finish requires precision at every step, and the key to that precision lies in one vital piece of equipment: the swinging vibrating screen. Whether you’re focused on getting that perfectly even coat or ensuring your automated system runs without a hitch, the right screen makes all the difference. In this post, I’ll explore how swinging vibrating screens play a critical role in maximizing powder coating efficiency, from ensuring uniform particle distribution to maintaining consistent powder flow in automated processes. I’ll also dive into the importance of selecting the right screen mesh size, and how making smart choices here directly impacts the quality of your coating. If you’re looking to optimize your powder coating operations and improve your finish quality, understanding the role of swinging vibrating screens is the first step to taking your process to the next level.
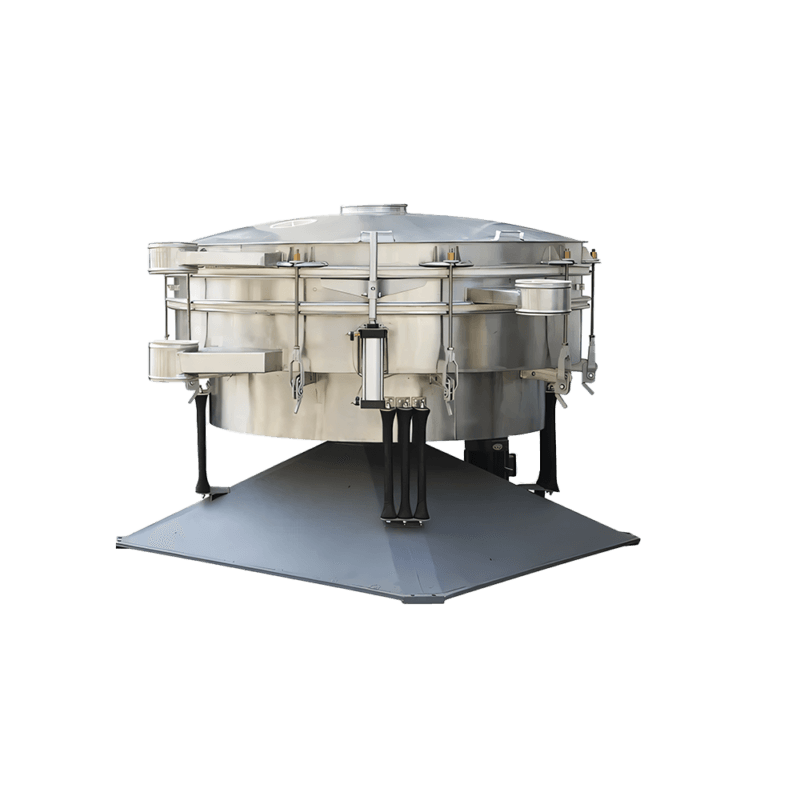
The Role of Swinging Vibrating Screens in Achieving Uniform Powder Coating
Uniformity is crucial in powder coating, and swinging vibrating screens are designed to deliver consistent results by ensuring an even distribution of powder particles. These screens use oscillatory motion to sift and classify powder particles, effectively separating any oversized or agglomerated particles that could lead to imperfections in the final coating. By filtering out inconsistencies, the screen ensures that only finely sized particles reach the coating surface, which results in a smoother, more even layer.
Additionally, swinging vibrating screens offer adjustable frequency and amplitude, allowing operators to fine-tune their setup for different powder types and coating requirements. This versatility is essential in achieving uniform coatings on surfaces of varying sizes, shapes, and materials. Whether you’re working with metallic, ceramic, or plastic surfaces, the precise control provided by swinging vibrating screens ensures that the coating adheres evenly, preventing issues such as uneven thickness, pinholes, or rough textures.
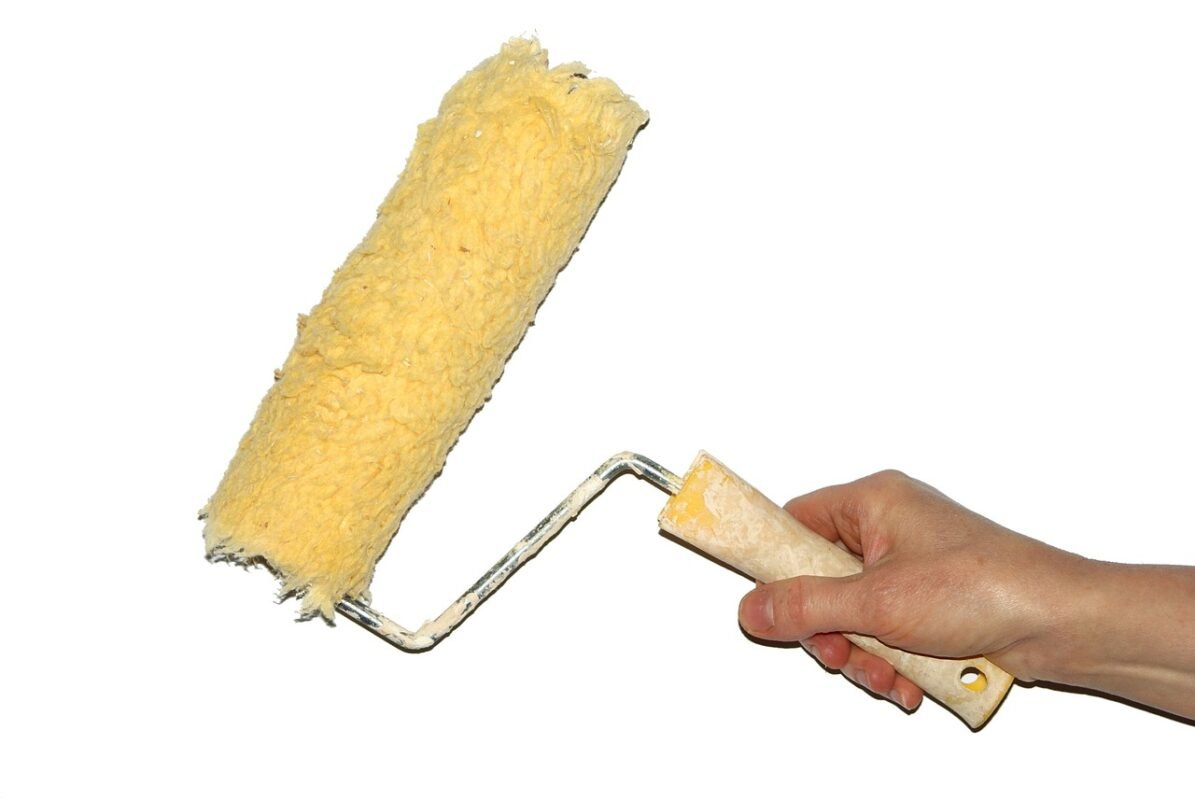
The Importance of Proper Screen Mesh Selection in Swinging Vibrating Screens for Powder Coating
One of the most critical aspects of achieving optimal performance with swinging vibrating screens is selecting the appropriate screen mesh size. The mesh size directly impacts the quality of the powder coating because it determines the size of the particles that can pass through the screen. For fine powder coatings, a smaller mesh size is generally preferred, as it helps achieve smoother, more even coatings. However, the mesh size must also be appropriate for the type of powder being used. For example, powders with larger particles require larger mesh sizes to avoid clogging the screen and ensuring consistent flow.
Proper mesh selection ensures that the right particle size reaches the coating equipment, which is especially important when working with specific coating thickness requirements. Using the wrong mesh size can result in uneven coating thickness, rough finishes, or clogging of the spray nozzles in automated systems. Understanding the characteristics of the powder being used and matching it to the correct screen mesh size is vital in maintaining quality control throughout the process.
How Swinging Vibrating Screens Optimize Powder Flow for Automated Powder Coating Systems
Automated powder coating systems require a consistent and steady flow of powder to function efficiently, and swinging vibrating screens play a critical role in maintaining this flow. These screens not only separate oversized particles but also ensure that the powder feed remains steady, preventing interruptions that could lead to uneven coatings or downtime. The oscillating motion of the swinging screens promotes continuous movement of powder, preventing buildup or blockages that could otherwise disrupt the process.
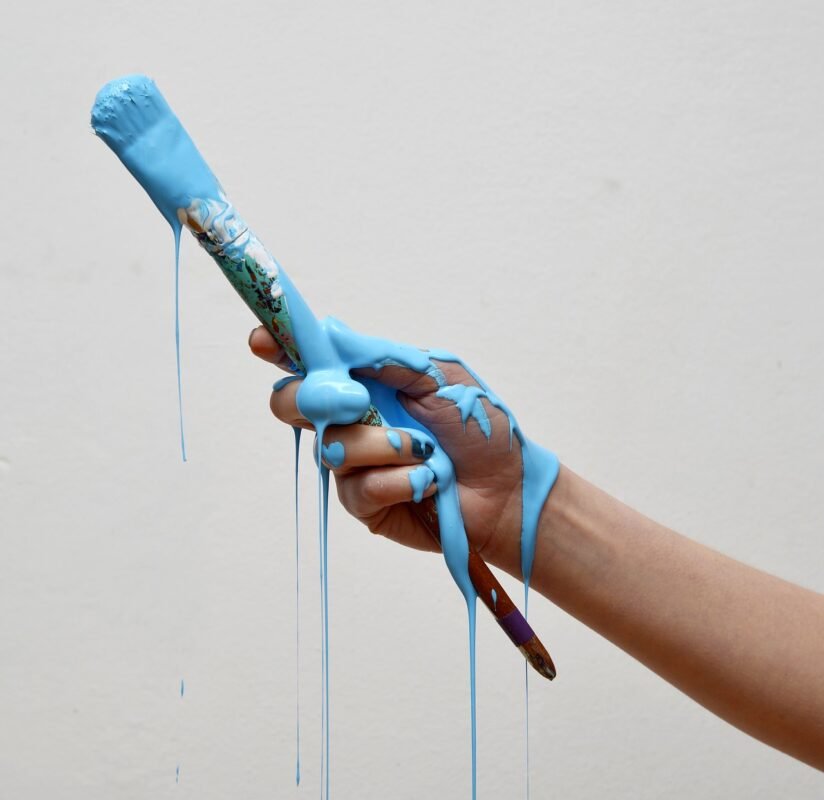
In an automated setting, ensuring a smooth and consistent powder flow is essential for maintaining production speed and coating quality. Swinging vibrating screens help automate this process by providing a uniform distribution of powder particles across the coating line. This consistent feed reduces the likelihood of clumping or excess buildup, which can cause irregularities in the coating. Additionally, swinging vibrating screens can be integrated with automated systems to adjust their settings in real-time, ensuring optimal performance as the coating process continues.
By optimizing powder flow, these screens not only enhance the efficiency of automated systems but also contribute to cost savings by reducing waste and minimizing downtime. In industrial-scale powder coating operations, this translates to higher throughput and better-quality finished products, making swinging vibrating screens an indispensable tool for achieving precision and consistency.
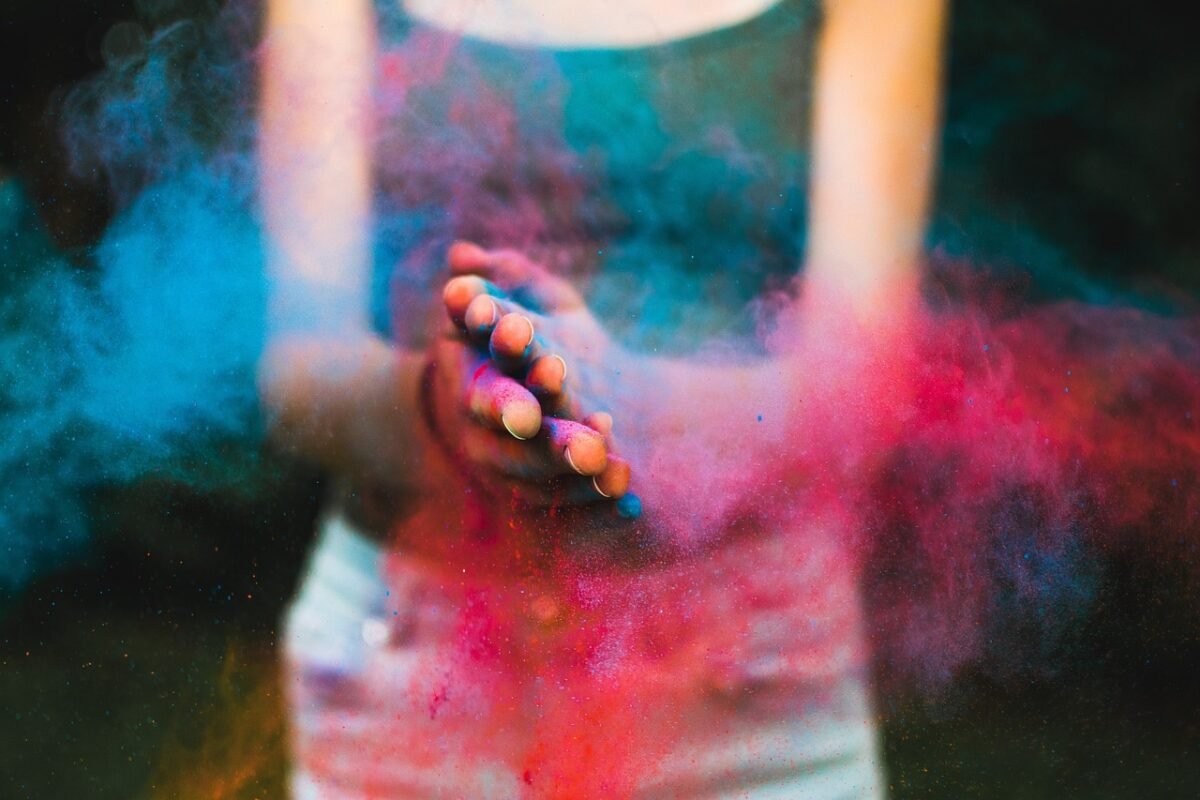
In conclusion, swinging vibrating screens are essential for ensuring precision and efficiency in powder coating processes. From achieving uniform coatings to optimizing powder flow in automated systems, the right screen mesh and setup can significantly impact the quality of the final product. By carefully selecting and fine-tuning your swinging vibrating screen, you can enhance your coating performance, reduce waste, and ensure consistent results across a wide range of industrial applications. Investing in the right equipment ultimately leads to better outcomes, higher productivity, and greater overall success in your powder coating operations.