When it comes to metal fabrication, precision is the name of the game. Whether you’re working on a large-scale industrial project or crafting custom pieces, the right bending machine can make all the difference. From mastering the art of metal manipulation to ensuring flawless bends across various thicknesses, understanding how to choose and use the best bending machines is crucial for any fabricator. In this post, I’ll dive deep into the world of bending machines, exploring their essential role in modern metal fabrication techniques, guiding you on selecting the perfect machine for different metal thicknesses, and sharing real-world case studies that showcase the success stories of professionals who have harnessed the power of these machines to achieve exceptional results. Whether you’re a seasoned metalworker or just starting out, this guide will help you take your metal fabrication skills to the next level.
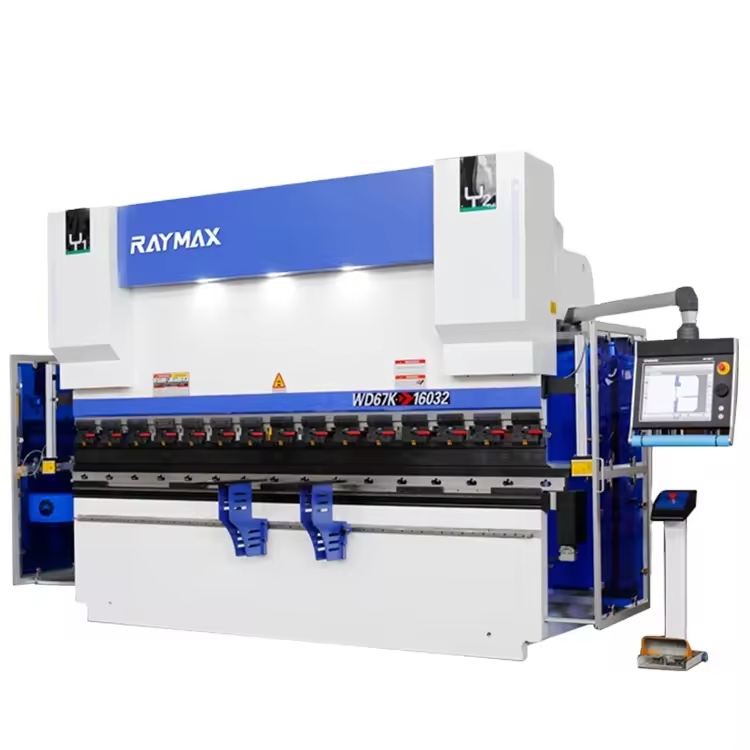
The Role of Bending Machines in Modern Metal Fabrication Techniques
Bending machines have become indispensable in the field of metal fabrication, playing a critical role in shaping metals into precise and complex forms that are essential in various industries. Modern fabrication techniques rely heavily on the capabilities of bending machines to create components with exact dimensions, angles, and radii, which are crucial for structural integrity and aesthetic appeal.
In the past, metal bending was often done manually, requiring skilled labor and time-consuming processes. However, as industries advanced, the demand for faster, more accurate, and consistent production grew. Bending machines emerged as a solution, automating the bending process and significantly increasing production efficiency. These machines are designed to handle a variety of metals, including steel, aluminum, and copper, allowing fabricators to work with different materials while maintaining high standards of precision.
The versatility of bending machines is another reason they are integral to modern fabrication techniques. They can perform a wide range of bending operations, from simple right-angle bends to more complex shapes, such as U-bends, V-bends, and custom profiles. This adaptability makes them suitable for various applications, including automotive parts, construction materials, and consumer goods. The ability to quickly switch between different bending operations without compromising on accuracy makes these machines a cornerstone of modern metalworking.
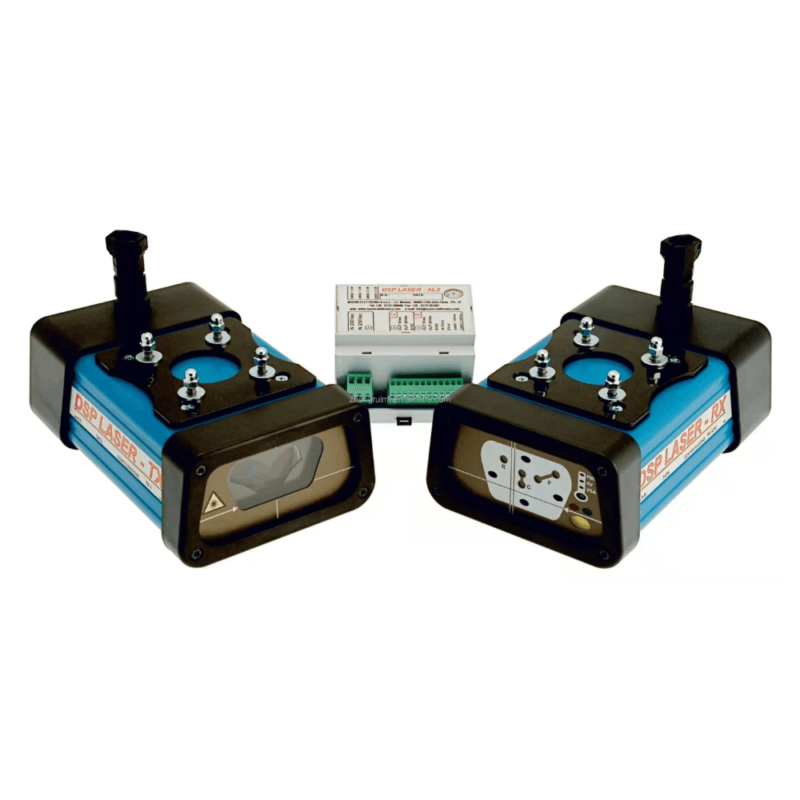
Moreover, the integration of advanced technology, such as CNC (Computer Numerical Control), has further enhanced the role of bending machines in metal fabrication. CNC technology allows for precise control over the bending process, enabling fabricators to produce highly accurate and repeatable results. This is especially important in industries where even the slightest deviation from specifications can lead to significant issues, such as aerospace and medical device manufacturing. By leveraging the capabilities of CNC bending machines, fabricators can meet stringent quality standards and deliver products that are both functional and aesthetically pleasing.
Choosing the Right Bending Machine for Various Metal Thicknesses
Selecting the appropriate bending machine for different metal thicknesses is crucial for achieving the desired results in metal fabrication. The thickness of the metal plays a significant role in determining the type of bending machine needed, as well as the specific settings and tools required for the job.
When dealing with thin metals, such as sheet metal, precision is key. Thin metals are more susceptible to deformation, so it is essential to use a bending machine that offers fine control over the bending process. Press brakes with adjustable settings are ideal for thin metals, as they allow the operator to apply the right amount of force without causing unwanted bends or warping. Additionally, tools like precision ground tooling can help ensure that the bends are clean and accurate.
For medium-thickness metals, a hydraulic press brake or a roll bending machine might be the best choice. These machines provide the necessary force to bend medium-thickness metals while maintaining control over the bend angle and radius. Hydraulic press brakes, in particular, offer a good balance between power and precision, making them suitable for a wide range of applications. It is important to consider the tonnage capacity of the machine, as this will determine its ability to handle different metal thicknesses.
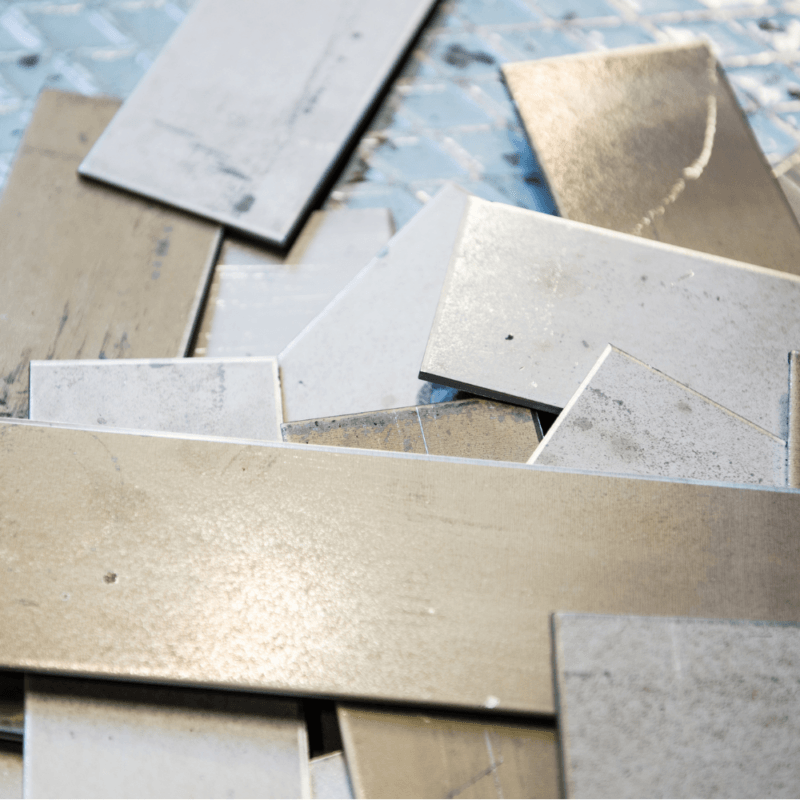
When working with thick metals, such as steel plates, a more robust machine is required. Heavy-duty hydraulic press brakes or plate rolling machines are often used for these applications. These machines are designed to exert significant force, allowing them to bend thick metals without causing cracks or fractures. However, it’s not just about having a powerful machine; the choice of tooling and machine settings is equally important. Thick metals require specific die and punch combinations to achieve the desired bend without compromising the material’s structural integrity. Properly selecting and setting up the machine ensures that even the thickest metals can be bent accurately and consistently.
Case Studies: Successful Metal Fabrication Projects Using Bending Machines
Real-world examples of successful metal fabrication projects highlight the importance of using the right bending machines and techniques. These case studies showcase how different industries have leveraged bending machines to achieve remarkable results, whether in terms of precision, efficiency, or innovation.
One notable case study comes from the automotive industry, where a manufacturer needed to produce complex exhaust systems with precise bends to fit within tight engine compartments. By using CNC-controlled press brakes, the company was able to achieve the required accuracy and repeatability, reducing waste and improving production efficiency. The use of advanced bending machines allowed the manufacturer to meet the stringent quality standards of the automotive industry while maintaining a competitive edge in the market.
Another example can be found in the construction industry, where a contractor was tasked with creating custom metal profiles for a modern architectural project. The project required a variety of metal thicknesses and shapes, from thin aluminum panels to thick steel beams. By employing a combination of press brakes and roll bending machines, the contractor was able to produce the required profiles with precision and consistency. This versatility allowed the contractor to meet the architect’s design specifications and deliver a finished product that was both functional and aesthetically pleasing.

In the aerospace industry, a company specializing in aircraft components faced the challenge of producing lightweight yet strong parts with complex geometries. Using a CNC press brake with advanced tooling, the company was able to bend high-strength aluminum alloys into precise shapes while maintaining the material’s integrity. The accuracy and consistency provided by the bending machine were critical in meeting the strict safety and performance standards required in aerospace manufacturing.
These case studies demonstrate that the successful application of bending machines in metal fabrication goes beyond simply having the right equipment. It involves understanding the specific requirements of each project, selecting the appropriate machine and tools, and fine-tuning the process to achieve the desired results. By doing so, fabricators can consistently produce high-quality metal products that meet or exceed industry standards.
In the world of metal fabrication, the right bending machine can make all the difference between a good project and a great one. Understanding the role these machines play, how to choose the right one for different metal thicknesses, and learning from real-world case studies provides invaluable insight into achieving precision and efficiency in every project. With the proper knowledge and tools, you can elevate your metalworking capabilities, ensuring that each bend is as flawless as the last. Invest in the right equipment, and your results will speak for themselves.