In the world of industrial screening, selecting the right equipment is crucial for optimizing productivity and maintaining consistent quality. One of the most effective tools for achieving this is the vibrating screen. But how exactly does it work, and how can you choose the right one for your specific production needs? In this post, I’ll break down the essentials of how vibrating screens work in various industrial applications, exploring the mechanics behind their operation and how they help improve screening efficiency. I’ll also guide you through the process of determining the ideal screen size for your unique production requirements, ensuring you achieve the perfect balance of throughput and separation. Whether you’re looking to boost productivity, reduce costs, or simply better understand the technology behind vibrating screens, this guide will give you the insights you need to make smarter, more informed decisions for your business.
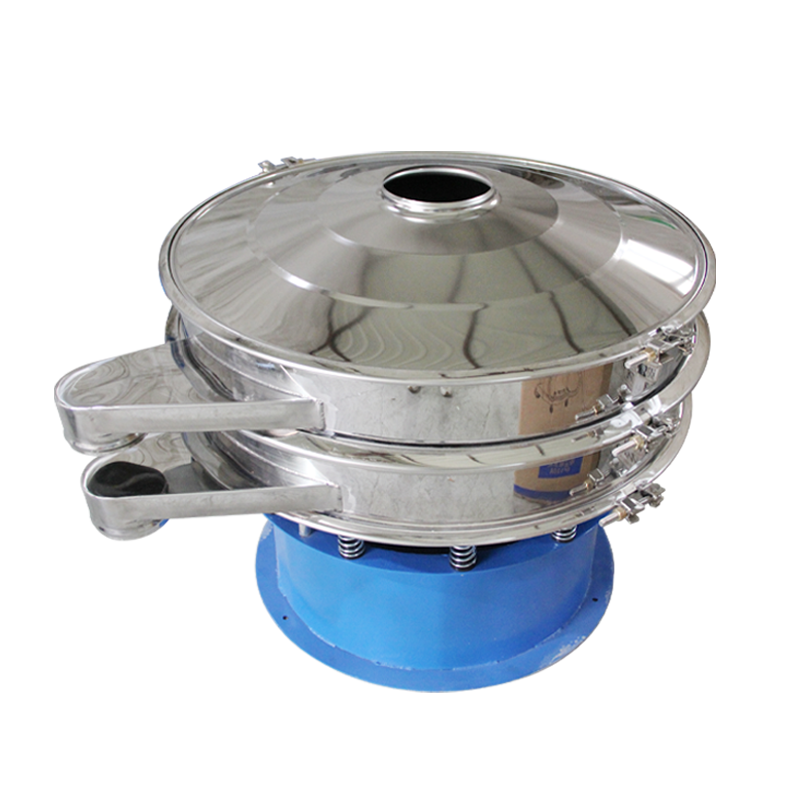
Understanding How a Vibrating Screen Works in Industrial Screening Applications
A vibrating screen is a mechanical device that uses vibration to separate materials of different sizes, typically in the mining, construction, recycling, or food processing industries. In industrial screening applications, its primary function is to sift, sort, and classify materials to meet specific size and purity standards.
At its core, a vibrating screen consists of a screen mesh that is vibrated at varying frequencies to agitate materials as they pass through it. This motion causes particles of different sizes to either fall through the screen or remain on top, depending on the size of the mesh openings.
There are two common types of motion used in vibrating screens:
- Linear motion: This type of motion is characterized by a straight-line movement, where materials are fed onto the screen, and vibrations move the materials from one end to the other. Linear motion is ideal for efficient separation and higher capacity in dry screening applications.
- Circular motion: This motion causes the material to move in a circular path, helping with the separation of larger and smaller particles. Circular vibrating screens are generally used when a high throughput is required, especially in wet screening applications or when handling sticky materials.
The working principle relies on excitation force, which is typically generated by a vibration motor. This motor drives the screen’s vibrating motion, causing the material on the screen to move forward and be sorted by particle size. The larger particles stay on top of the mesh, while smaller particles pass through, allowing for efficient classification.

In summary, vibrating screens function as separation tools by creating specific vibrations that help sort materials based on size. Their primary use in industrial applications is for material screening, where a fine level of separation is essential, such as in the grading of aggregates, recycling of materials, or even in food processing applications like flour and spice sieving.
2. How to Determine the Ideal Vibrating Screen Size for Your Production Needs
Choosing the right vibrating screen size for your production needs is a critical decision that impacts both the efficiency and effectiveness of your operation. The ideal screen size depends on several factors, including material characteristics, desired output, and screening goals.
Here are the key considerations when determining the ideal vibrating screen size:
- Material Type and Characteristics: Different materials require different screen sizes to ensure optimal separation. For instance, if you’re processing heavy, abrasive materials like sand or gravel, you may need a screen with larger openings and a thicker mesh. For finer particles, such as powder or small seeds, a smaller mesh with finer openings will be required. The hardness and moisture content of the material also play a role—wet or sticky materials may require specialized screens with unique mesh coatings or specific vibration motions to prevent clogging.
- Throughput Capacity: The size of the vibrating screen directly impacts how much material can be processed in a given time. When selecting the screen size, you’ll need to consider the volume of material you expect to process per hour or day. Larger screens with bigger surface areas allow for greater throughput, but they may also require more space and higher energy consumption. It’s essential to balance the size of the screen with the required production capacity.

- Desired Separation and Purity: For some applications, achieving precise separation is crucial. If you’re looking to sort materials into a narrow range of sizes, you may need a screen with smaller mesh openings or even a multi-deck screen that provides multiple layers of separation. On the other hand, if a broader classification is sufficient, a larger mesh might be more appropriate.
- Vibrating Screen Deck Design: The number of decks (or layers) can also affect the selection of the right size. Multi-deck screens allow for multi-stage separation in one machine, increasing throughput and providing more efficient processing for materials that require different grades of separation.
- Available Space: In some cases, the physical space available for installing the vibrating screen may limit your options. If space is a constraint, you might opt for a compact, high-performance vibrating screen that can handle the necessary throughput without taking up much floor space.
Key Tip: When determining the vibrating screen size, it’s essential to perform tests using your material to understand the screen’s performance and make adjustments based on the results. Consulting with manufacturers or experts in industrial screening can also provide valuable insights into selecting the correct screen for your needs.
3. How Vibrating Screens Improve Screening Efficiency and Productivity
Vibrating screens are integral to enhancing efficiency and productivity in industrial screening applications. By providing high throughput, precise separation, and consistent results, these machines contribute to streamlining operations in various industries. Here’s how they improve screening efficiency and overall productivity:
- Increased Throughput: One of the primary benefits of using a vibrating screen is its ability to handle large volumes of material at once. The high-frequency vibrations and adjustable screening motion allow for faster material movement, enabling the screen to process more material per unit of time. This increases overall throughput, which is critical for industries that require fast processing, such as mining, construction, and food production.
- Improved Separation and Accuracy: Vibrating screens provide a precise separation of particles based on size, improving the quality of the final product. For example, in food processing, separating fine flour from larger particles or sifting spices for impurities can be done with a high degree of accuracy. With the ability to adjust the vibration frequency and amplitude, operators can fine-tune the screen for optimal separation, ensuring better material purity and less wastage.
- Customization for Specific Applications: Many vibrating screens come with customizable features such as adjustable mesh size, multiple decks, and varying vibration amplitudes, allowing them to be tailored for specific applications. This customization ensures that the screen performs at its best for particular materials or production goals, maximizing both efficiency and productivity.
- Energy Efficiency: Modern vibrating screens are designed with energy efficiency in mind. By using vibrating motors that consume less energy while still providing powerful screening capabilities, businesses can reduce their operational costs and improve overall efficiency. Energy-efficient screens also reduce the environmental impact of industrial operations, contributing to sustainability efforts.

- Reduced Maintenance Downtime: Vibrating screens are designed to be durable and low-maintenance, which helps to keep production lines running smoothly. With proper care, these screens can operate for extended periods with minimal downtime. Their robust construction and reliable performance also reduce the frequency of repairs and replacement, increasing overall productivity and reducing maintenance costs.
- Scalability: As businesses grow and production volumes increase, vibrating screens can easily be scaled to meet these demands. Larger, more efficient screens can be installed to increase throughput without needing to significantly redesign the entire system. This scalability is beneficial for industries with fluctuating production needs, as vibrating screens can be upgraded to accommodate more extensive operations.
In conclusion, vibrating screens improve screening efficiency by offering precise particle separation, boosting throughput, and reducing downtime. Their versatility, scalability, and customizable features help industries meet their production goals while maintaining consistent quality.
Conclusion
Vibrating screens play a pivotal role in industrial screening applications by ensuring efficient separation and sorting of materials. Understanding how they work, choosing the right screen size for your production needs, and recognizing how they contribute to increased efficiency and productivity are essential steps for optimizing your operation. By selecting the appropriate vibrating screen for your specific requirements, you can enhance the quality of your output, streamline production processes, and maximize your facility’s overall productivity.
In conclusion, choosing the right vibrating screen for your industrial screening needs is essential to improving efficiency, ensuring precise separation, and optimizing productivity. By understanding how vibrating screens operate, selecting the appropriate screen size for your material, and recognizing the benefits of increased throughput and reduced downtime, you can make more informed decisions for your business. With the right vibrating screen, you can not only achieve high-quality results but also streamline your operations, boost production speed, and reduce long-term costs. Take the time to carefully assess your specific needs, and invest in a vibrating screen that will support your growth and success in the competitive industrial landscape.