The Importance of Sieving in Capsule Production
Why Precision Sieving Matters in Pharmaceutical Manufacturing
Precision sieving is a cornerstone of pharmaceutical manufacturing, ensuring that the ingredients used in capsule production are uniformly sized and free from contaminants. In the world of pharmaceuticals, where the smallest variance in composition can have significant implications, sieving becomes an essential process. Accurate sieving not only ensures the proper flowability of powders but also influences the bioavailability and potency of the final product. For instance, improper particle size distribution can result in clumping, inconsistent dosing, or poor capsule filling, leading to unreliable results and reduced therapeutic efficacy.

The Role of Sieving in Ensuring Capsule Filler Efficiency
Efficient capsule filling is a critical step in pharmaceutical production, and sieving plays an indispensable role in this process. Sieving helps to separate fine particles and larger agglomerates, ensuring that only the optimal powder enters the capsule. When powders are properly sieved, they flow more easily into the capsules, reducing the chances of blockages or jamming within the filling machines. This not only improves throughput but also enhances the overall efficiency of the manufacturing process, enabling pharmaceutical companies to meet production targets without compromising quality.
How Contaminant-Free Powders Improve Capsule Quality
Contaminants in pharmaceutical powders can severely affect the quality and safety of capsules. Sieving plays a pivotal role in removing unwanted particles such as foreign matter, fines, or impurities that could otherwise taint the powder. By employing high-precision sieving techniques, manufacturers can produce cleaner, purer powders that meet stringent quality standards. The removal of contaminants ensures that the capsules maintain their integrity and deliver consistent dosages, ultimately safeguarding the health of end users and supporting regulatory compliance.
Key Sieving Equipment for Capsule Fillers
Stainless Steel Mesh Screens: A Crucial Component for Accurate Sieving
Stainless steel mesh screens are widely regarded as one of the most effective tools for sieving powders in pharmaceutical applications. Their corrosion-resistant properties ensure longevity, while the fine, consistent mesh sizes allow for precise separation of particles. These screens come in a variety of grades and mesh sizes to suit different powder types and desired separation levels. By selecting the right mesh screen, manufacturers can guarantee that only the properly sized particles pass through, ensuring uniformity in the final capsule product and preventing any inconsistencies that could affect quality or performance.
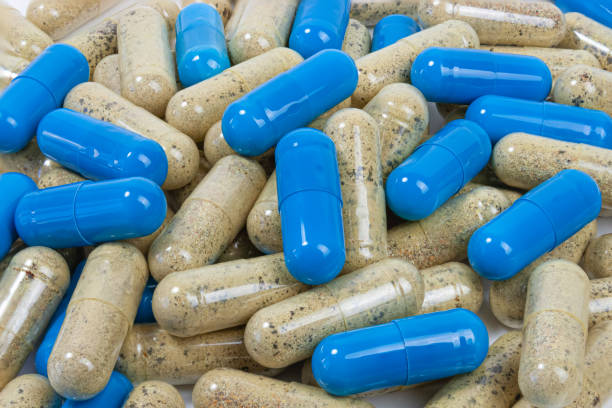
Vibratory Sieves vs. Traditional Sieving Methods: Which is Best?
The debate between vibratory sieves and traditional sieving methods is one that many pharmaceutical manufacturers face when optimizing their production processes. Traditional sieving methods often rely on manual shaking or mechanical agitation, which can be labor-intensive and prone to inconsistencies. In contrast, vibratory sieves use high-frequency vibrations to create a consistent flow of powders through the screen, offering superior performance in terms of separation efficiency and speed. Vibratory sieves are particularly beneficial when dealing with fine powders or high volumes of material, as they prevent clogging and ensure a more uniform result. While traditional methods might still have a place in smaller-scale operations, vibratory sieves are often the preferred choice for larger pharmaceutical manufacturers seeking efficiency and precision.
High-Efficiency Pharmaceutical Sieving Equipment for Bulk Powder Processing
When dealing with large volumes of pharmaceutical powders, high-efficiency sieving equipment becomes crucial. Equipment like automatic sieve machines, centrifugal sifters, and multi-deck sieves can handle large batches of powder in a fraction of the time it would take traditional sieving methods. These systems are designed to operate continuously, with minimal downtime, and can process powders at a higher rate without sacrificing accuracy. The use of high-efficiency sieving equipment is essential for pharmaceutical manufacturers looking to scale up production while maintaining stringent quality control and minimizing the risk of contamination.
Optimizing Sieving Equipment for Superior Capsule Filling
Choosing the Right Mesh Size for Pharmaceutical Powders
Selecting the right mesh size is paramount to achieving optimal powder separation. In pharmaceutical manufacturing, the mesh size dictates the size of particles that are allowed to pass through. For finer powders, a smaller mesh size (higher mesh count) is required, while coarser powders necessitate larger mesh openings. Using the wrong mesh size can lead to ineffective sieving, resulting in powders that are either too coarse or too fine for the intended application. Therefore, understanding the characteristics of the powder, such as particle size distribution and flowability, is essential when selecting an appropriate mesh size to ensure uniformity and consistency in the final capsule.
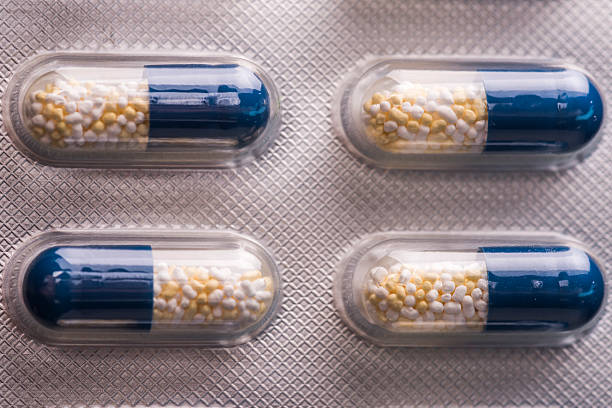
Best Practices for Maintaining Sieving Equipment in Capsule Production
Routine maintenance of sieving equipment is crucial to maintaining its performance and longevity. Regular cleaning of mesh screens and parts, calibration of vibration frequencies, and inspection for wear and tear are necessary to ensure that sieves operate efficiently. Preventative maintenance can reduce the risk of unexpected breakdowns, which could lead to production delays and costly downtime. It is also essential to keep the sieving environment clean and free from contaminants, as external dirt and dust can negatively impact the sieving process. Proper maintenance helps extend the lifespan of sieving equipment, ensuring that it continues to deliver precise, reliable results throughout its operational life.
Enhancing Sieving Performance with Advanced Screening Technologies
Recent advancements in screening technologies have significantly enhanced the performance of sieving equipment. Techniques such as ultrasonic sieving and air jet sieving can be integrated into traditional sieving processes to improve particle separation. Ultrasonic sieving, for example, uses high-frequency sound waves to break up agglomerates and reduce clumping, allowing powders to pass through more easily. These advanced technologies help to achieve even higher levels of separation, efficiency, and consistency, making them invaluable tools for modern pharmaceutical manufacturers.
Ensuring Compliance and Quality in Pharmaceutical Sieving
Meeting Industry Standards for Sieving in Capsule Manufacturing
In the pharmaceutical industry, adhering to established standards is essential for ensuring product safety and quality. Sieving equipment used in capsule manufacturing must comply with international standards such as those set by the US Pharmacopeia (USP), the European Pharmacopoeia (EP), and ISO regulations. These standards dictate specifications for equipment performance, cleanliness, and material compatibility. By following these guidelines, manufacturers can ensure that their sieving processes meet the necessary criteria for producing safe, effective pharmaceuticals.
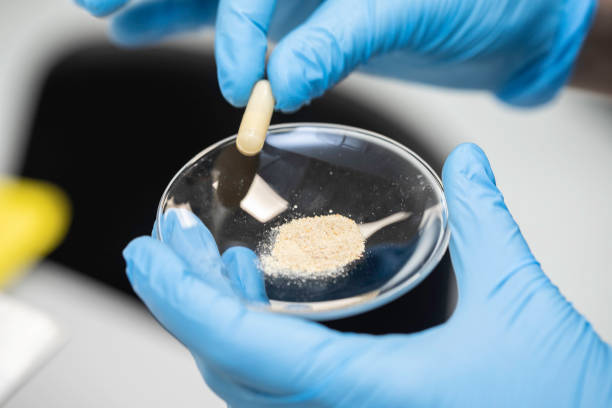
Regulatory Considerations for Pharmaceutical Sieving Equipment
Pharmaceutical sieving equipment must meet stringent regulatory requirements to ensure safety, efficacy, and consistency in capsule production. Regulatory bodies like the FDA and EMA set clear guidelines regarding equipment design, validation, and performance testing. It is crucial that manufacturers document and validate their sieving processes to demonstrate compliance with these regulations. Failure to comply with these requirements could result in penalties, product recalls, or even the suspension of production.
How Proper Sieving Supports GMP and FDA Compliance
Good Manufacturing Practice (GMP) guidelines, as outlined by the FDA, require pharmaceutical manufacturers to maintain strict control over all production processes, including sieving. Proper sieving ensures that only uniform, contaminant-free powders enter the filling machines, which is critical for maintaining consistency in the final product. By ensuring that sieving equipment is calibrated, maintained, and validated, manufacturers can demonstrate their commitment to quality and compliance, thereby safeguarding patient safety and meeting the necessary regulatory standards.
Future Trends in Pharmaceutical Sieving for Capsule Fillers
Automation and AI in Sieving Technology for Enhanced Accuracy
The integration of automation and artificial intelligence (AI) into sieving technology is poised to revolutionize pharmaceutical manufacturing. AI-powered sieving systems can monitor and adjust parameters such as vibration frequency, mesh tension, and particle size distribution in real-time, optimizing the sieving process. Automated systems can also provide predictive maintenance alerts, ensuring that sieving equipment operates at peak efficiency and preventing downtime. This shift towards automation will further streamline production, reduce human error, and improve the accuracy and consistency of capsule filling.
Innovations in Ultrasonic and Multi-Frequency Sieving Systems
Ultrasonic sieving has already proven to be a game-changer in pharmaceutical powder processing, but future innovations are set to enhance its capabilities even further. Multi-frequency sieving systems, which utilize a combination of different frequencies, can achieve higher precision in separating powders of varying sizes and densities. These innovations will allow for more efficient processing of difficult-to-sieve powders, such as those with a high moisture content or sticky characteristics. As these technologies continue to evolve, they will provide pharmaceutical manufacturers with even greater control over the sieving process, enabling them to meet increasingly demanding production requirements.
The Future of Sieving Equipment in High-Speed Capsule Production
As the demand for high-speed capsule production continues to rise, sieving equipment will need to evolve to keep pace with the increased production volumes. Future sieving systems will likely incorporate more advanced automation, higher throughput capacities, and even more precise particle separation techniques. The ability to maintain consistent quality at high speeds will be essential for meeting market demands while ensuring that pharmaceutical products remain safe, effective, and compliant with regulatory standards. The future of sieving equipment lies in its ability to combine speed with accuracy, offering manufacturers a competitive edge in the fast-paced pharmaceutical industry.