Understanding Coating Efficiency and Its Importance
Why Coating Efficiency Matters in Production Processes
Coating efficiency is a critical component in manufacturing processes across many industries, from pharmaceuticals to food production. The ability to apply coatings consistently and uniformly not only enhances the visual appeal of products but also ensures their functionality. When coatings are applied efficiently, production times are reduced, material waste is minimized, and the final product meets quality standards more reliably. Low coating efficiency, on the other hand, can lead to uneven surfaces, excess material usage, or even compromised product performance. In industries where precision is key, like electronics or medical devices, coating efficiency becomes even more important to meet stringent regulatory and quality requirements.
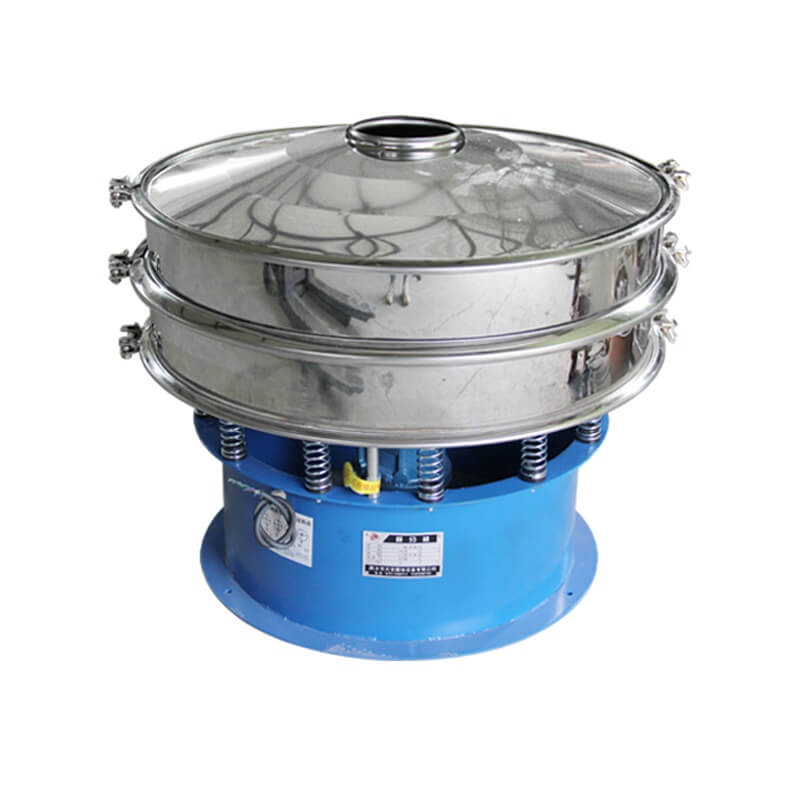
The Role of Coating in Product Quality and Performance
Coating is often the final touch in creating a product that is both aesthetically pleasing and functional. Whether it’s providing a protective layer, enhancing durability, or ensuring that the product meets specific regulatory standards, coatings play a fundamental role. For instance, in the food industry, coatings may serve as protective barriers to extend shelf life or add flavor, while in the electronics industry, coatings prevent corrosion and wear. The uniformity and consistency of the coating directly impact the longevity, performance, and safety of the product. A well-applied, high-quality coating guarantees the product performs optimally throughout its life cycle.
Key Factors Influencing Coating Efficiency
Several factors contribute to the overall efficiency of coating processes. One of the most important is the precision with which the coating is applied. Whether through spray techniques or powder coating, the consistency of application can determine how effectively the coating adheres and covers the substrate. The quality of the materials used, such as the coating substance itself and any pre-coating treatments, also plays a significant role in the outcome. Environmental conditions, including humidity and temperature, must be controlled for optimal results. Finally, the equipment used to apply and cure the coating is crucial in achieving a balance between speed, precision, and quality, with vibrating screens and sifters being vital components in this equation.
The Science Behind Vibrating Screens and Sifters
How Vibrating Screens Improve Coating Uniformity
Vibrating screens are an invaluable tool in the production process, especially when uniformity is key. These screens use vibration to separate and classify materials according to size and consistency. In coating processes, vibrating screens ensure that the particles of the coating material are evenly distributed, preventing clumping or agglomeration that could affect the final finish. By separating larger particles from finer ones, vibrating screens ensure that only the correct particle size enters the coating process, which is crucial for achieving a uniform and smooth finish. The controlled vibration also aids in the even application of powder coatings, preventing issues like uneven coating thickness or surface defects.
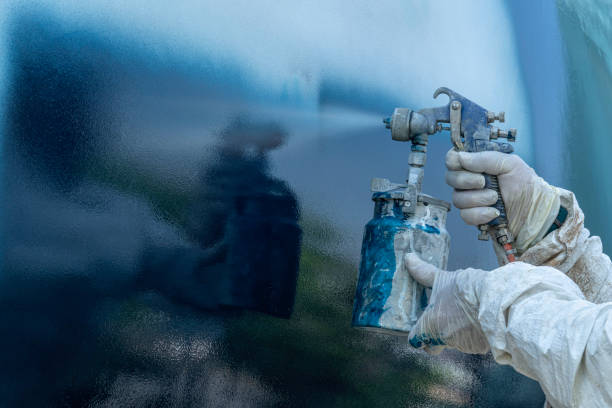
The Mechanism of Sifters in Enhancing Coating Precision
Sifters play a vital role in refining the coating material, ensuring only the finest, most consistent particles are used. A sifter, often integrated with a vibrating screen, uses a mesh to separate particles based on size, ensuring that the powder or granules applied to the product are uniform in shape and size. This precision is essential when dealing with sensitive coating applications, where the smallest inconsistencies can lead to visible flaws or functional issues. Sifters ensure that the particles passing through are of the appropriate size to achieve the desired coating thickness and texture. In essence, sifters refine the coating material before it’s applied, enhancing the overall quality of the finished product.
Vibrating Screens vs Traditional Sieving: A Comparative Analysis
While traditional sieving methods have been in use for centuries, vibrating screens have rapidly gained prominence due to their efficiency and ability to handle larger volumes of material. Traditional sieving typically relies on a static mesh through which material is manually or gravity-fed, a process that can lead to clogging and inconsistent results. In contrast, vibrating screens use mechanical motion to agitate the material, allowing for more consistent flow and better separation of particles. Vibrating screens are more effective at preventing material buildup and clogging, ensuring continuous processing without downtime. Additionally, they provide better control over the sieving process, enabling finer and more accurate separations. This results in a more consistent coating material that enhances product quality.
Optimizing Coating Processes with Vibrating Screens and Sifters
How to Select the Right Sieving Equipment for Coating Applications
Selecting the right sieving equipment for coating applications is crucial to optimizing the overall production process. Factors such as the type of coating material, the required particle size, and the volume of material to be processed will dictate the choice of sieving equipment. Vibrating screens are ideal for processing larger quantities of powder coatings or granules, while smaller-scale operations may benefit from rotary sifters. The mesh size must be selected to match the particle size distribution of the coating material; too fine a mesh could lead to clogging, while too coarse a mesh may fail to capture unwanted large particles. Furthermore, the equipment should be designed to handle the chemical properties of the coating material, particularly in cases where the material is sensitive or reactive.
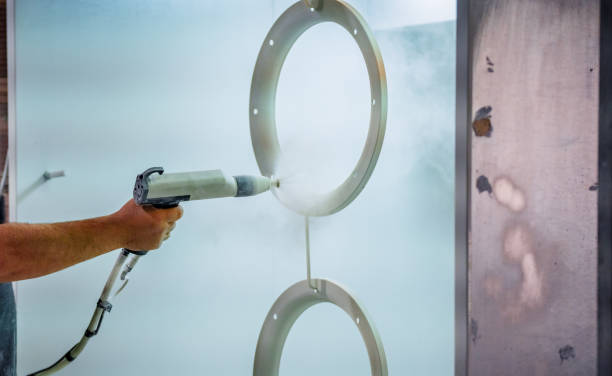
Best Practices for Integrating Vibrating Screens into Coating Lines
To achieve maximum efficiency, vibrating screens must be seamlessly integrated into coating lines. One of the best practices is to ensure that the screens are positioned at the optimal point in the process. For example, placing vibrating screens before the coating application ensures that only the right particle sizes are fed into the system. Additionally, it’s important to monitor the vibration parameters, such as frequency and amplitude, to ensure they are fine-tuned for the material being processed. Regular maintenance, such as checking for wear on the mesh and ensuring the vibration mechanism is functioning correctly, will also ensure long-term reliability. Finally, integrating automated controls to adjust the vibration intensity and throughput based on real-time conditions can further optimize the process.
Troubleshooting Common Issues in Coating Efficiency with Sifters
Despite their effectiveness, sifters and vibrating screens can sometimes experience issues that may impact coating efficiency. One of the most common problems is clogging, particularly when the mesh is not the correct size or when the coating material contains moisture. To resolve this, it’s important to regularly check the mesh and replace it when necessary. Another issue that can arise is inconsistent vibration, which can lead to uneven material flow or failure to properly separate particles. In this case, adjusting the motor settings or checking for mechanical faults can help. In some cases, changes in the material, such as its moisture content or chemical composition, may require adjustments in the sieving equipment or vibration settings to ensure continued efficiency.
Maximizing Output with Maintenance and Calibration
How Regular Maintenance Ensures Long-Term Coating Efficiency
Regular maintenance is the cornerstone of sustained coating efficiency. Vibrating screens and sifters experience wear and tear over time, particularly due to the constant motion and abrasive materials they handle. To avoid unexpected downtime, it’s essential to schedule regular maintenance checks, including cleaning the mesh, inspecting the motors, and lubricating moving parts. A well-maintained vibrating screen will continue to perform at its best, ensuring consistent product quality and preventing costly repairs or replacements. Additionally, regular maintenance helps identify potential problems before they escalate, allowing for timely interventions that preserve both efficiency and equipment lifespan.

Calibration Tips to Optimize Vibrating Screen and Sifter Performance
Calibration is a key factor in ensuring vibrating screens and sifters operate at their peak performance. Adjusting the vibration settings, such as amplitude and frequency, to suit the specific coating material is essential for achieving optimal separation and uniformity. The calibration should also extend to the feed rate and mesh tension, ensuring that the material flows evenly and without obstruction. Routine checks and recalibrations can ensure that the equipment remains aligned with the production goals, adapting to changes in material properties or coating specifications. Calibration should be done periodically, especially when switching between different coating materials or production runs.
Understanding the Role of Screen Mesh Size in Coating Quality
The screen mesh size is one of the most important factors influencing coating quality. A finer mesh allows for a more precise separation of particles, ensuring that only the desired size enters the coating process. However, if the mesh is too fine for the material being processed, it can cause clogging and reduce efficiency. Conversely, a mesh that is too coarse will allow large particles to pass through, leading to inconsistencies in the coating. Regularly checking and adjusting the mesh size to suit the specific needs of the coating material is key to maintaining high-quality outputs. The right mesh size ensures that only the perfect particle size reaches the coating line, resulting in a flawless, consistent finish every time.