Activated Carbon Sieving Equipment: Balancing Capacity and Durability
Activated carbon sieving equipment plays a pivotal role in the processing of activated carbon, ensuring that it meets the necessary quality standards for a wide range of industrial applications. The challenge lies in balancing two critical factors: capacity and durability. Capacity determines how much material can be processed in a given timeframe, while durability ensures that the equipment can handle continuous use without compromising its performance or lifespan. Achieving this balance is key to maximizing operational efficiency and minimizing maintenance costs. In this article, we will explore how to effectively balance these factors to optimize your sieving equipment’s performance.
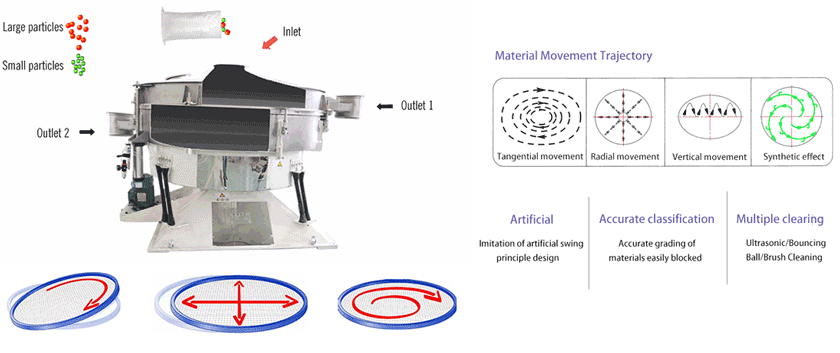
Understanding the Importance of Capacity and Durability in Sieving Equipment
The Role of Capacity in Activated Carbon Sieving Equipment
Capacity is often the first consideration when selecting sieving equipment for activated carbon. In industrial processes, high throughput is essential for maintaining productivity. The capacity of sieving equipment is typically measured by its ability to handle large volumes of material per hour, which directly impacts overall production efficiency. However, an excessively high capacity can sometimes lead to issues such as material clogging or uneven distribution of particles. Therefore, it is essential to select equipment with the right balance of throughput to ensure the process runs smoothly without unnecessary delays or bottlenecks.
The need for capacity depends largely on the scale of operations and the specific use case. For example, a facility processing small batches may require equipment with lower throughput, while a large-scale production plant would need sieving equipment capable of handling vast quantities of activated carbon efficiently. It is also essential to align the equipment’s capacity with the desired particle size separation, as different sizes may require different levels of processing power.
Why Durability Matters for Long-Term Performance
Durability is just as important as capacity when selecting sieving equipment for activated carbon. The physical properties of activated carbon, particularly its abrasiveness, can lead to wear and tear on equipment over time. Without durability, frequent breakdowns, repairs, and equipment replacements become costly and disruptive to operations. Sieving equipment that is built to withstand continuous use without significant degradation ensures consistent performance and minimizes downtime.
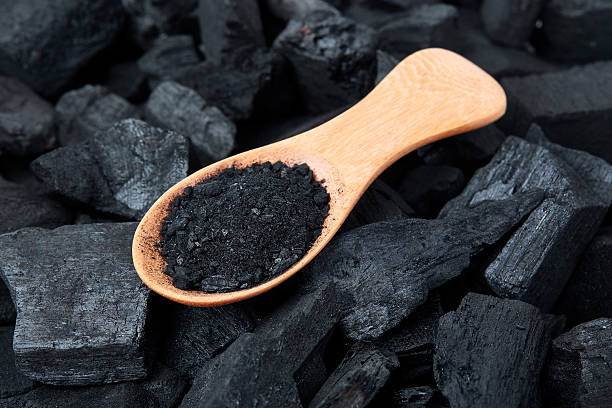
The durability of sieving equipment is determined by factors such as material construction, design quality, and the capacity to handle various operational conditions. For instance, activated carbon may come in varying densities and particle sizes, and if the sieving equipment cannot withstand the impact of harder or coarser particles, its components will wear out more quickly. Therefore, choosing sieving equipment made from high-quality materials designed to resist abrasive wear is critical for ensuring long-term performance.
How Capacity and Durability Impact Operational Efficiency
The balance between capacity and durability directly influences the operational efficiency of a sieving system. If the equipment is designed for high throughput but lacks durability, it may experience more frequent breakdowns, which in turn reduces overall efficiency. On the other hand, if the equipment is overly durable but lacks capacity, it may slow down the sieving process, leading to delays in production.
By choosing equipment that is both highly durable and capable of handling the required capacity, operators can achieve optimal efficiency. The key is to ensure that the equipment can handle the load without compromising its long-term ability to perform effectively. This balance minimizes downtime, reduces maintenance costs, and enhances productivity across the entire sieving operation.
Key Factors Influencing Capacity and Durability
Material Properties of Activated Carbon and Their Effect on Sieving
Activated carbon is typically a porous, granular material with a highly abrasive surface. This abrasiveness can cause significant wear on sieving equipment, especially when processing large volumes over long periods. The size, shape, and density of the particles also affect the sieving process. Fine particles may clog screens, while larger, denser particles may damage the sieve mesh or result in inefficient separation.
Understanding the specific material properties of activated carbon is critical when selecting sieving equipment. The equipment must be robust enough to handle the unique challenges posed by activated carbon, such as its tendency to break into smaller fragments or its potential to clog the screen.
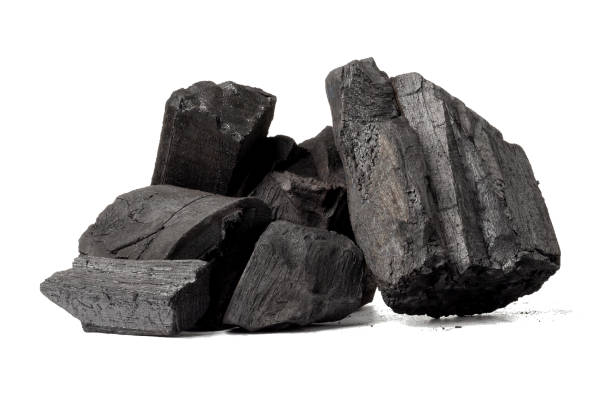
The Impact of Screening Mesh and Mesh Size on Capacity
Screening mesh is one of the most vital components of sieving equipment. The size of the mesh opening directly impacts the capacity of the equipment to process activated carbon. Smaller mesh sizes are ideal for separating fine particles, but they can also limit throughput as they may become clogged more quickly. Larger mesh sizes allow for higher capacity and throughput, but they may not provide the fine separation required for certain applications.
Selecting the correct mesh size is essential for achieving a balance between capacity and the desired level of particle separation. The mesh size should align with the specific requirements of the activated carbon being processed, taking into consideration its particle size distribution and the desired end product.
Choosing Durable Materials for Sieving Equipment
Durability of sieving equipment is heavily influenced by the materials used in its construction. Common materials for sieving equipment include stainless steel, carbon steel, and polyurethane, each offering distinct advantages and limitations. Stainless steel, for example, is resistant to corrosion and wear, making it an ideal choice for environments where high levels of abrasion are expected. Polyurethane, on the other hand, offers excellent flexibility and impact resistance, which can help prolong the lifespan of sieves used in high-impact sieving applications.
When selecting materials for sieving equipment, it is crucial to consider the operational environment, including factors such as humidity, temperature, and the abrasiveness of the material being processed. The right material choice can enhance durability and ensure that the equipment performs optimally throughout its lifecycle.
How Vibrational Force and Frequency Affect Equipment Lifespan
Vibrational force and frequency are key factors in the performance of sieving equipment, particularly when working with activated carbon. The frequency of vibration determines how well the material moves across the screen, while the amplitude of the vibration controls the level of agitation. This agitation helps to separate particles of varying sizes and ensures that the sieving process remains efficient.
However, excessive vibration or incorrect frequency settings can lead to premature wear on the equipment. Over time, this can reduce the lifespan of the sieve mesh, cause fatigue in the equipment’s structural components, and increase the frequency of repairs. Proper tuning of the vibrational force and frequency is essential to balance capacity with durability, ensuring that the equipment runs efficiently without compromising its longevity.
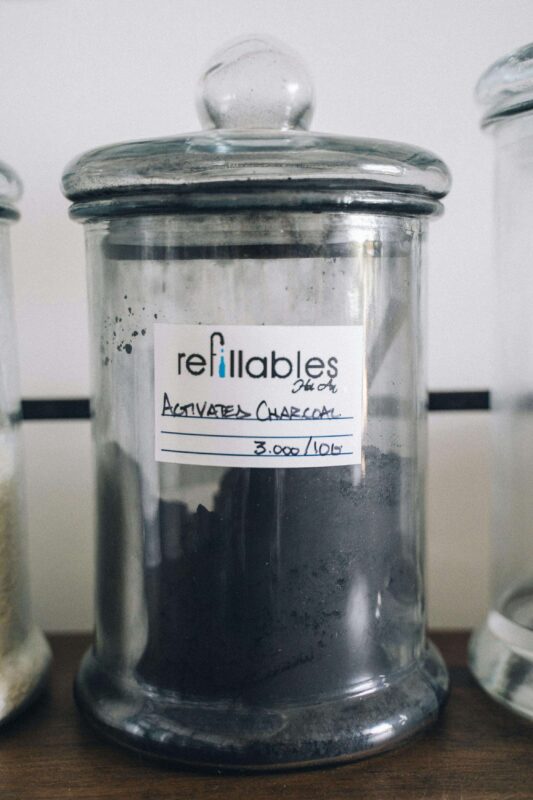
Optimizing Capacity Without Compromising Durability
Balancing High Throughput with Equipment Longevity
The most effective sieving systems are those that can handle high throughput without sacrificing durability. Achieving this balance requires careful selection of equipment designed for the unique demands of activated carbon processing. For high-capacity operations, it’s essential to choose sieving equipment that can maintain consistent performance under heavy loads while minimizing wear and tear.
For example, investing in higher-quality mesh materials, such as those made of stainless steel or other abrasion-resistant alloys, can extend the lifespan of the equipment while allowing for higher capacity. Additionally, implementing effective vibration control and monitoring systems can prevent overloading and ensure that the equipment operates at optimal efficiency.
Enhancing Sieving Performance Through Regular Maintenance
Regular maintenance is key to ensuring that sieving equipment performs optimally for an extended period. Monitoring the condition of the mesh, checking for wear and tear, and cleaning the equipment regularly are vital practices for preserving both capacity and durability. Additionally, periodically replacing worn components and making necessary adjustments to the equipment’s settings can prevent breakdowns and extend the life of the equipment.
A proactive maintenance strategy not only boosts the performance of sieving equipment but also helps identify and address potential issues before they escalate into more significant problems, thereby reducing downtime and improving overall productivity.
Customizing Sieving Equipment for Specific Activated Carbon Needs
Activated carbon comes in a wide range of grades, each with distinct processing requirements. Customizing sieving equipment to handle specific types of activated carbon ensures that the capacity and durability are optimized for the material at hand. Custom features, such as specialized mesh configurations, vibration settings, and material construction, can significantly enhance the sieving process and ensure the equipment meets the specific demands of activated carbon processing.
Customizing sieving equipment also allows for better scalability, enabling businesses to adapt their sieving systems as production needs change over time. Whether it’s for increased throughput or greater material durability, tailored solutions ensure that the equipment remains effective throughout its lifecycle.
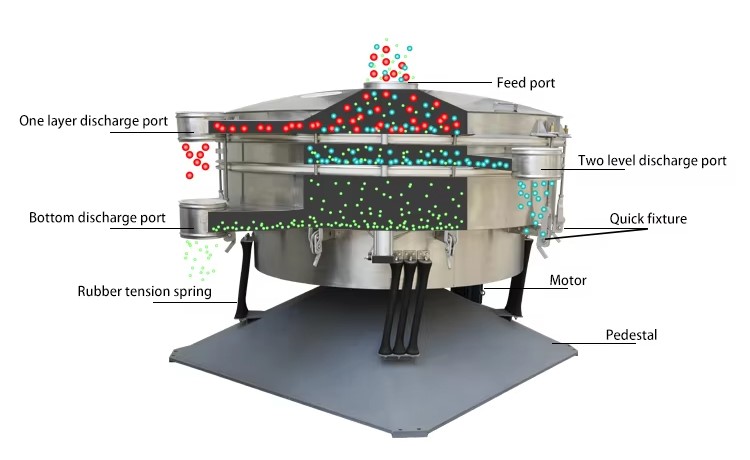
Choosing the Right Sieving Equipment for Your Activated Carbon Process
Assessing Your Specific Capacity Requirements
Before selecting sieving equipment, it’s important to assess the specific capacity requirements for your activated carbon process. This involves considering factors such as the volume of material to be processed, the desired throughput, and the intended application of the activated carbon. Once these factors are determined, you can select equipment that meets your needs for both capacity and durability.
Selecting Durable Sieving Equipment for High-Volume Operations
For operations that involve high-volume processing, choosing sieving equipment made from durable materials and designed for heavy-duty use is essential. High-capacity systems with reinforced structures and robust components can withstand the constant demand of high-volume production while maintaining their performance over time.
Tips for Improving the Efficiency and Durability of Sieving Equipment
To maximize the efficiency and durability of your sieving equipment, consider incorporating advanced features like automated monitoring systems, vibration dampening technologies, and regularly scheduled maintenance protocols. These practices can help detect wear early, prevent overloading, and optimize the sieving process, ensuring that both capacity and durability are maintained throughout the lifespan of the equipment.
By balancing these considerations, businesses can select the most appropriate sieving equipment for their activated carbon processing needs, achieving both high capacity and long-term durability.