When it comes to achieving flawless powder consistency, choosing the right sieve shaker is critical. Whether you’re dealing with fine powders for pharmaceuticals, food processing, or industrial applications, the precision of your particle sizes can make or break the quality of your end product. In this post, I’ll walk you through how sieve shakers ensure consistent powder particle size, why understanding mesh sizes is essential for controlling fineness, and how advanced sieve shaker technology can streamline your screening process. If you’re looking for the perfect powder, the right sieve shaker is your key to success.
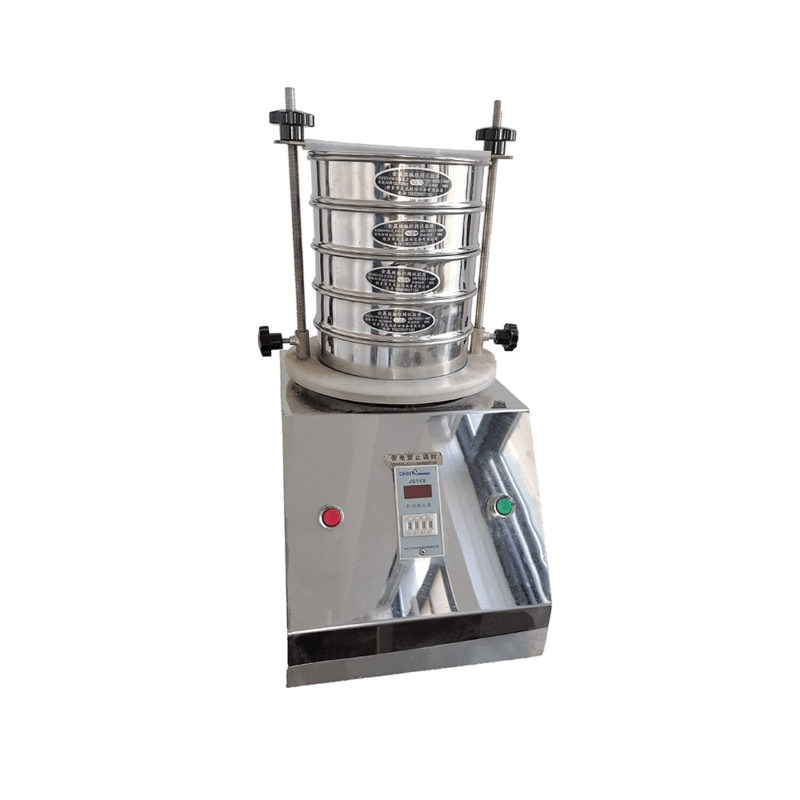
How Sieve Shakers Ensure Consistent Powder Particle Size
Sieve shakers are essential tools in powder processing, designed to provide uniformity in particle size distribution. Consistency in powder particle size is crucial for various applications, from pharmaceuticals to food processing, as it affects the final product’s quality, efficacy, and performance.
Sieve shakers work by utilizing a combination of mechanical vibration and shaking motion to promote effective separation of powder particles based on size. When a sample is placed in a stack of sieves, each with different mesh sizes, the shaker oscillates to facilitate the movement of particles through the screens. Smaller particles pass through the finer mesh while larger ones remain on top, ensuring a precise and repeatable particle size distribution. This consistent size is essential for achieving desired physical and chemical properties in the final products, such as flowability, mixing, and dissolution rates.
Investing in a high-quality sieve shaker can significantly improve the efficiency of your powder processing operations, reduce variability, and enhance product quality. Whether you are involved in R&D or large-scale manufacturing, understanding how sieve shakers function and the benefits they offer is fundamental to optimizing your processes.
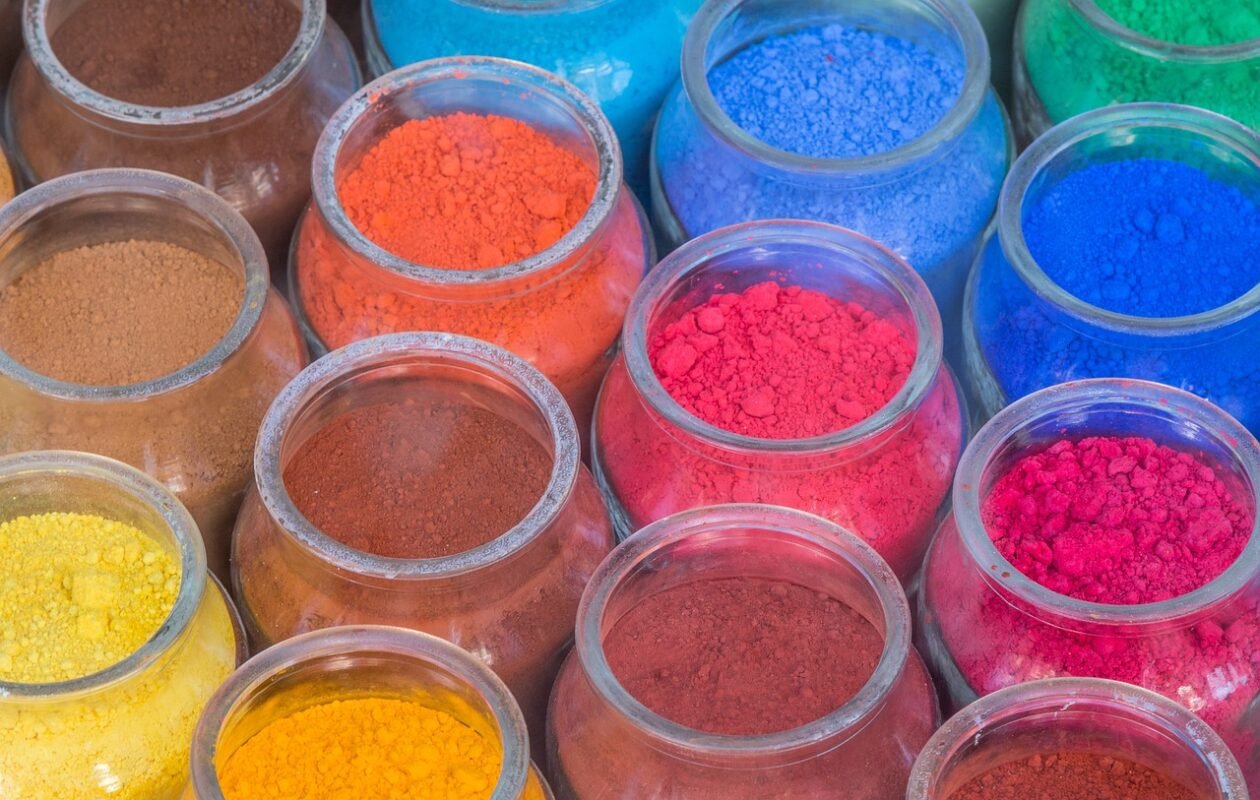
2. Understanding Mesh Sizes: How Sieve Shakers Influence Powder Fineness
Mesh size is a critical factor when selecting sieve shakers, as it directly affects the fineness of the powder produced. Mesh size refers to the number of openings per inch in the sieve, and it determines the particle size that can pass through the screen. Understanding mesh sizes is essential for achieving the desired fineness of your powders.
Larger mesh sizes have more openings and will allow smaller particles to pass through, while smaller mesh sizes will retain larger particles. For example, a sieve with a mesh size of 100 means that there are 100 openings per square inch, effectively filtering out particles larger than the specified size. Conversely, a mesh size of 50 allows larger particles to pass through, resulting in coarser powders.
When selecting a sieve shaker, it’s vital to consider the application and the required particle size distribution. A well-chosen mesh size can ensure that the powder meets specific standards for consistency and quality. Additionally, using a range of mesh sizes in a sieve stack allows for a thorough analysis of particle size distribution, helping to identify the ideal formulation and processing parameters for different materials.
3. The Importance of Calibration and Maintenance in Sieve Shakers
Calibration and regular maintenance of sieve shakers are critical for ensuring accuracy and reliability in powder screening processes. Over time, wear and tear can affect the shaker’s performance, leading to inconsistencies in particle size distribution.
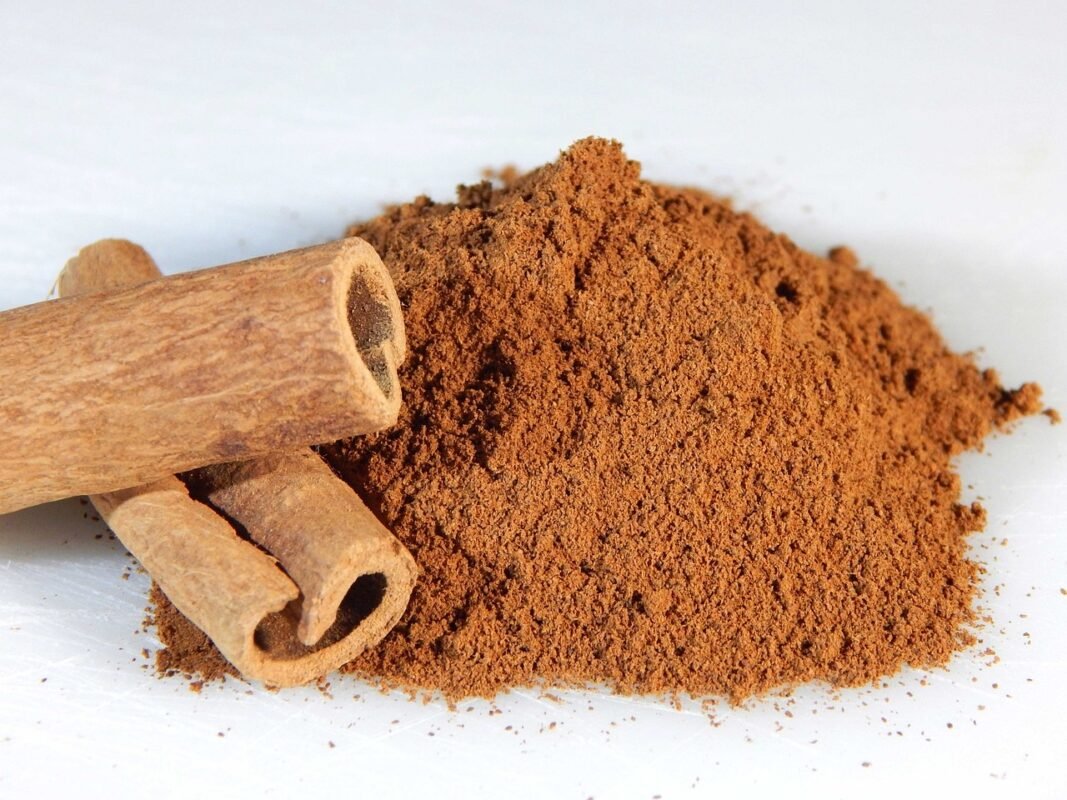
Calibration involves setting the shaker to a known standard to ensure it produces reliable and repeatable results. This process helps to identify any deviations in performance that could compromise the quality of the final product. Regularly checking the calibration against standard reference materials allows for early detection of issues, ensuring that the shaker operates within specified tolerances.
Maintenance is equally important. This includes routine cleaning of sieves to prevent cross-contamination, inspecting for wear or damage, and lubricating moving parts to ensure smooth operation. Proper maintenance extends the lifespan of the equipment and guarantees that the sieve shaker continues to deliver precise and consistent results.
By prioritizing calibration and maintenance, operators can achieve optimal performance from their sieve shakers, leading to improved product quality and reduced waste in powder processing operations.
Conclusion
In summary, sieve shakers play a vital role in ensuring consistent powder particle size and fineness, which are essential for high-quality product outcomes. Understanding mesh sizes and implementing proper calibration and maintenance practices will enhance the efficiency and effectiveness of your powder processing operations. Investing in the right sieve shaker tailored to your specific needs can ultimately lead to significant improvements in product quality and operational productivity.