Understanding Fine Mesh Sieving and Its Importance in Vitamin Powder Production
What is Fine Mesh Sieving and How Does It Work?
Fine mesh sieving is a crucial process in the production of vitamin powders, ensuring the final product meets the required standards of purity and consistency. Essentially, sieving involves the use of a screen with fine, precise mesh openings that allow only particles smaller than the mesh size to pass through. This process effectively separates smaller vitamin particles from larger contaminants or clumps that may form during production. It relies on both gravity and mechanical vibration to push the powder through the mesh, leaving behind impurities that are too large to pass through.
This technology is particularly important for industries that require a high degree of accuracy and uniformity in particle size, like vitamin powder production, where even the slightest impurity can affect both the potency and safety of the final product.

The Role of Fine Mesh Sieving in Ensuring Product Purity and Consistency
Fine mesh sieving plays a pivotal role in achieving product purity by effectively removing foreign materials, such as dust, undissolved particles, or agglomerated lumps, that may be present in the raw ingredients. It helps in refining the texture of the powder, ensuring that only the finest, most uniform particles remain. By ensuring that the vitamin powder is homogeneous, sieving promotes product consistency, which is vital for ensuring that each batch meets stringent quality standards.
Consistency in particle size distribution not only enhances the efficacy of the product but also influences its dissolution rates, bioavailability, and shelf-life. The use of fine mesh sieving allows manufacturers to maintain these consistent quality parameters over large production runs, which is critical for consumer safety and product reliability.
Key Benefits of Fine Mesh Sieving for Vitamin Powder Quality
The primary benefit of fine mesh sieving lies in its ability to deliver high-quality vitamin powders. By filtering out coarse particles, the process results in a finer, more uniform powder. This not only ensures a smoother texture but also guarantees better dissolution when mixed into foods or supplements. Additionally, sieving minimizes the risk of contamination by removing extraneous materials, which is particularly important in the nutraceutical industry, where purity is paramount.
Moreover, the precise sizing of particles can influence the powder’s bioavailability. Finer powders often have increased surface areas, leading to faster absorption in the body. This is particularly important for vitamins, where the consistency of particle size can affect how efficiently the body absorbs nutrients.
How Fine Mesh Sieving Enhances the Efficiency of Vitamin Powder Processing
Reducing Contaminants and Impurities in Vitamin Powder
The primary objective of fine mesh sieving in vitamin powder production is to remove contaminants and impurities. In raw materials, even trace amounts of unwanted substances can compromise the quality of the final product. Sieving helps eliminate oversized particles, including dirt, metallic residues, or larger agglomerated particles that may result from the manufacturing process. This ensures that the vitamin powder is pure, safe for consumption, and free from any potentially harmful substances.
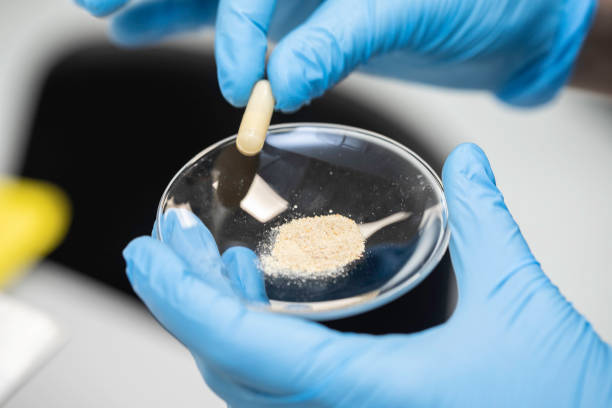
In addition, sieving reduces the likelihood of cross-contamination with other substances, ensuring that each batch remains consistent and meets the necessary safety regulations.
Improving Flowability and Uniformity of Vitamin Powder
A key challenge in vitamin powder production is maintaining optimal flowability and uniformity in the powder’s consistency. Sieving helps achieve this by breaking up any clumps or agglomerates that may have formed during storage or processing. This is essential, as uneven powders can lead to inconsistent dosing in the final product.
With better flowability, manufacturers can ensure a more efficient production process, leading to fewer blockages and less downtime. Furthermore, uniformity in particle size makes the powder easier to handle during packaging and delivery, improving operational efficiency.
Maximizing Yield with Precise Sieving Technology
Fine mesh sieving enhances processing efficiency by ensuring that more of the material passes through the mesh without being discarded. This helps maximize yield, as less material is lost during the sieving process. By using the correct mesh size, manufacturers can ensure that almost all of the usable vitamin powder is sieved and collected, improving the overall yield from raw materials and contributing to cost-effectiveness in production.
Precise sieving technology also ensures that waste material is minimized, reducing both costs and the environmental impact of the production process.
The Impact of Fine Mesh Sieving on the Vitamin Powder Market in India
Meeting Increasing Demand for High-Quality Vitamin Powder in India
India’s vitamin and dietary supplement market has seen significant growth in recent years, driven by increasing health awareness and rising disposable income. As the demand for high-quality vitamin powders rises, the need for efficient production methods becomes more critical. Fine mesh sieving addresses this demand by providing a reliable and efficient method to refine the powder’s texture and remove impurities, ensuring that products meet the high standards expected by consumers.
With a growing population and a focus on wellness, India is positioning itself as a leader in the global vitamin powder market. Fine mesh sieving plays a central role in meeting both domestic and international demand by enhancing the quality of vitamin powders.
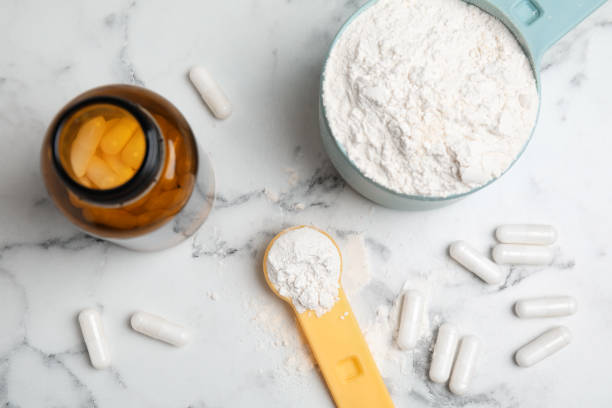
Fine Mesh Sieving as a Competitive Edge in the Indian Market
In an increasingly competitive market, manufacturers who can offer high-quality vitamin powders with superior purity and consistency will have a distinct advantage. Fine mesh sieving technology allows manufacturers to produce powders that meet the highest industry standards, which can differentiate their products in a crowded market. By investing in advanced sieving technology, companies in India can stand out, gaining a reputation for quality and precision.
This competitive edge is crucial as more consumers in India turn to vitamin powders for their nutritional needs, and demand for premium products continues to rise.
Addressing Regulatory Standards with Fine Mesh Sieving
India’s regulatory landscape for food and health supplements is becoming increasingly stringent, particularly concerning the quality and safety of vitamin products. Fine mesh sieving plays a significant role in helping manufacturers meet these regulations. By ensuring that vitamin powders are free from contaminants and impurities, sieving contributes to compliance with safety standards set by the Food Safety and Standards Authority of India (FSSAI) and other regulatory bodies.
Adhering to these regulations not only safeguards consumer health but also strengthens the reputation of manufacturers in both domestic and international markets.
Selecting the Right Sieving Equipment for Vitamin Powder Production
Choosing the Optimal Mesh Size for Vitamin Powder Sieving
The right mesh size is essential for achieving the desired quality and consistency in vitamin powder production. Smaller mesh sizes are typically used to achieve finer powders, but this must be balanced with the ability to handle larger volumes of material efficiently. Too fine a mesh may lead to clogging, while too coarse a mesh may allow undesirable particles to pass through.
Selecting the optimal mesh size requires an understanding of both the material’s characteristics and the desired end product. Manufacturers must carefully consider factors such as the particle size distribution of the raw materials and the specific type of vitamin powder being produced.
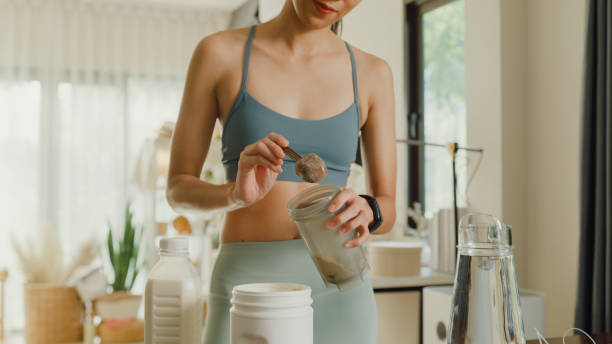
Factors to Consider When Selecting Sieving Equipment for Vitamin Powder
Choosing the right sieving equipment involves evaluating factors such as capacity, ease of maintenance, vibration control, and mesh durability. The equipment must be able to handle the specific volume of vitamin powder produced while maintaining a high level of accuracy and efficiency. Durability is crucial, especially when dealing with fine powders, as the sieves must withstand the mechanical stresses of constant operation without degradation.
Moreover, sieving machines with adjustable vibration levels allow for customization based on the characteristics of the powder being processed. This flexibility ensures optimal sieving performance and improves overall production efficiency.
Maintenance Tips for Ensuring Long-Term Sieving Efficiency
Regular maintenance of sieving equipment is essential to ensure long-term efficiency. Over time, mesh screens can become clogged or damaged, affecting their ability to separate fine particles. It is important to regularly clean and inspect sieves, replacing any damaged parts to avoid contamination or inefficient sieving.
Additionally, calibrating the equipment periodically can ensure that the sieves remain accurate and efficient throughout their operational life. Proper maintenance minimizes downtime and ensures that the sieving process remains optimal for consistent quality production.
The Future of Fine Mesh Sieving in India’s Vitamin Powder Industry
Emerging Technologies in Fine Mesh Sieving for Vitamin Powder
The future of sieving technology looks promising, with innovations such as ultrasonic sieving and automated systems making significant strides. These advanced technologies offer improved efficiency, greater precision, and the ability to handle more complex materials. For the vitamin powder industry, these innovations could result in higher throughput, reduced waste, and enhanced product quality.
Ultrasonic sieving, for instance, utilizes high-frequency sound waves to improve the sieving process, enabling even finer separation without compromising speed or throughput. As these technologies become more widely available, they will continue to revolutionize the vitamin powder production process in India.
Innovations in Sieving Equipment and Their Potential Impact on the Industry
In the coming years, sieving equipment is likely to become more automated, incorporating sensors and smart technology to optimize performance. These innovations can improve the monitoring of sieving operations, ensuring that parameters such as vibration intensity and mesh integrity are consistently maintained. This automation will lead to reduced human error, improved operational efficiency, and better overall product quality.
How Fine Mesh Sieving Will Continue to Shape the Future of Vitamin Powder Production in India
As India’s vitamin powder industry grows, the role of fine mesh sieving in ensuring consistent, high-quality products will only become more important. With increased demand for purity and efficiency, sieving technology will continue to evolve, pushing the boundaries of what’s possible in terms of speed, precision, and scalability. As new innovations in sieving equipment emerge, India’s vitamin powder producers will be well-positioned to meet the challenges of a growing and highly competitive market.